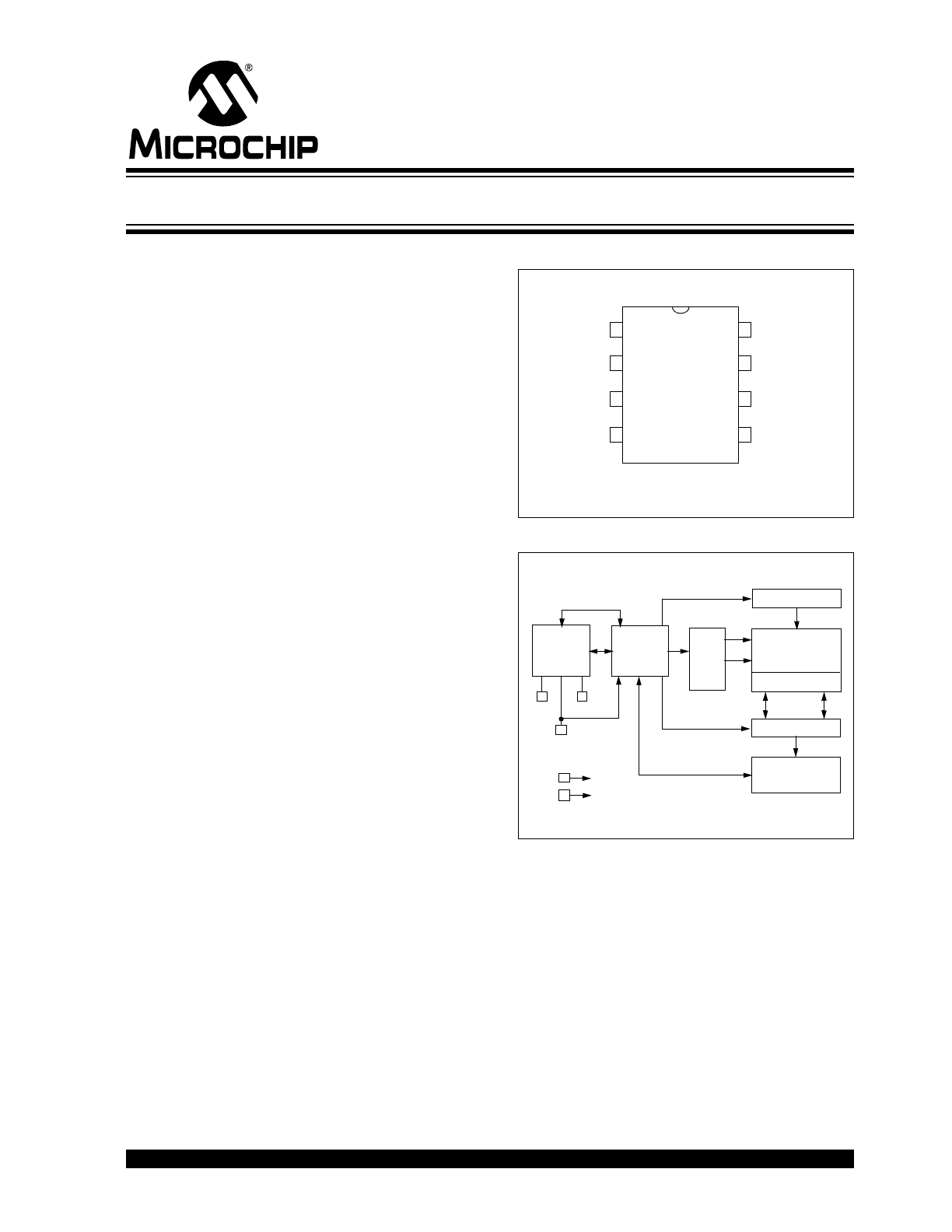
© 2007 Microchip Technology Inc.
DS21683B-page 1
24LC22A
Features:
• Single Supply with Operation Down to 2.5V
• Supports Enhanced EDID™ (E-EDID™) 1.3
• Completely Implements DDC1™/DDC2™
Interface for Monitor Identification, Including
Recovery to DDC1
• 2 Kbit Serial EEPROM Low-Power CMOS
Technology:
- 1 mA typical active current
- 10 uA standby current typical at 5.5V
• 2-Wire Serial Interface Bus, I
2
C
™
Compatible
• 100 kHz (2.5V) and 400 kHz (5V) Compatibility
• Self-Timed Write Cycle (including Auto-Erase)
• Page-Write Buffer for up to Eight Bytes
• 1,000,000 Erase/Write Cycles
• Data Retention >200 years
• ESD Protection >4000V
• 8-pin PDIP and SOIC Packages
• Available Temperature Ranges:
• Pb-Free and RoHS Compliant
Description:
The Microchip Technology Inc. 24LC22A is a 256 x 8-
bit dual-mode Electrically Erasable PROM. This device
is designed for use in applications requiring storage
and serial transmission of configuration and control
information. Two modes of operation have been imple-
mented: Transmit-Only mode (1 Kbit) and Bidirectional
mode (2 Kbit). Upon power-up, the device will be in the
Transmit-Only mode, sending a serial bit stream of the
memory array from 00h to 7Fh, clocked by the VCLK
pin. A valid high-to-low transition on the SCL pin will
cause the device to enter the Transition mode, and look
for a valid control byte on the I
2
C bus. If it detects a
valid control byte from the master, it will switch into
Bidirectional mode, with byte selectable read/write
capability of the entire 2K memory array using SCL. If
no control byte is received, the device will revert to the
Transmit-Only mode after it receives 128 consecutive
VCLK pulses while the SCL pin is idle. The 24LC22A is
available in standard 8-pin PDIP and SOIC packages.
Package Types
Block Diagram
- Industrial (I)
-40°C to
+85°C
PDIP/SOIC
24
LC
22A
*NC
*NC
*NC
V
SS
1
2
3
4
8
7
6
5
V
CC
VCLK
SCL
SDA
* Pins labeled ‘NC’ has no internal connections
HV Generator
EEPROM
Array
Page Latches
YDEC
XDEC
Sense AMP
R/W Control
Memory
Control
Logic
I/O
Control
Logic
SDA
SCL
V
CC
V
SS
VCLK
2K VESA
®
E-EDID™ Serial EEPROM
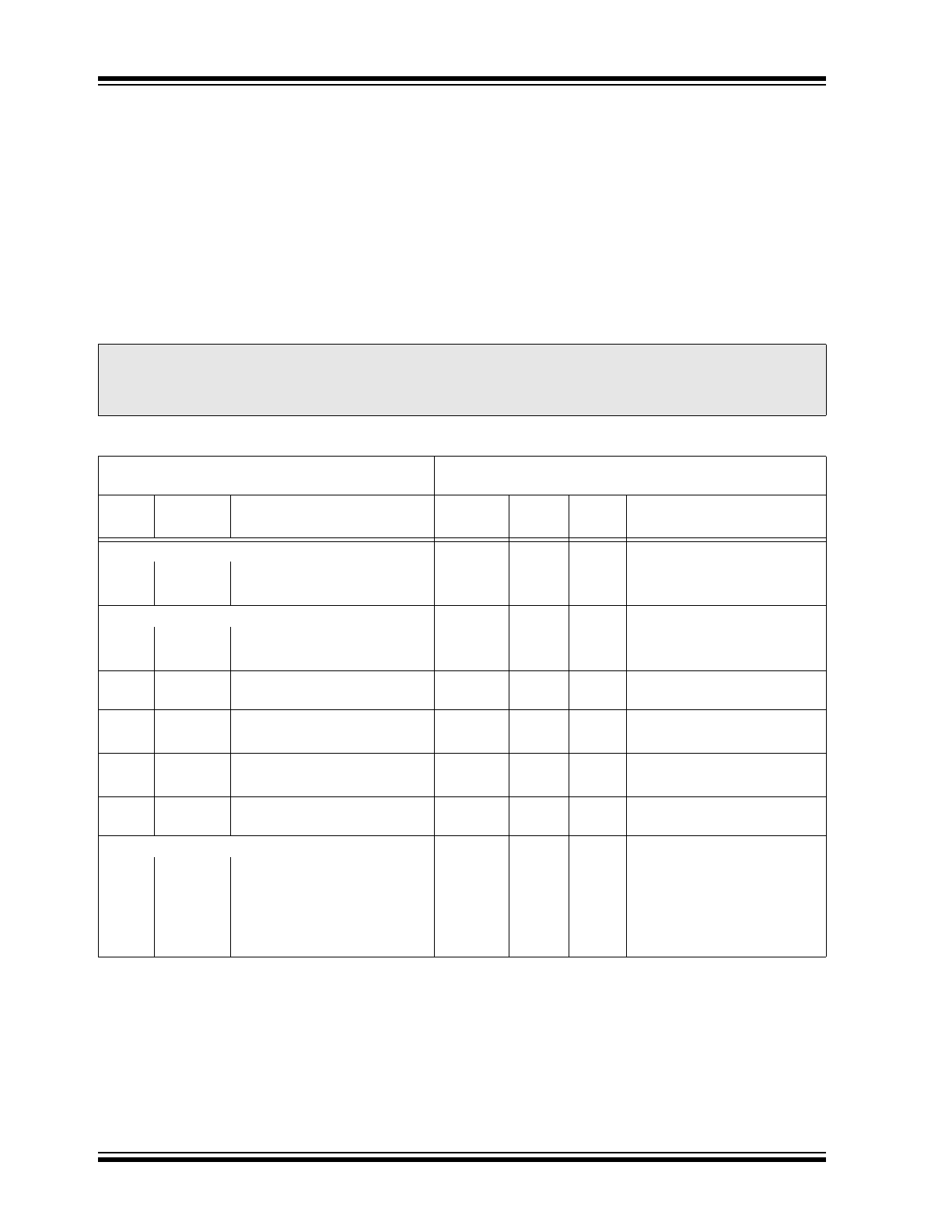
24LC22A
DS21683B-page 2
© 2007 Microchip Technology Inc.
1.0
ELECTRICAL
CHARACTERISTICS
Absolute Maximum Ratings†
V
CC
.............................................................................................................................................................................7.0V
All inputs and outputs w.r.t. V
SS
......................................................................................................... -0.6V to V
CC
+1.0V
Storage temperature ...............................................................................................................................-65
°C to +150°C
Ambient temp. with power applied ..........................................................................................................-40
°C to +125°C
Soldering temperature of leads (10 seconds) .......................................................................................................+240
°C
ESD protection on all pins
......................................................................................................................................................≥ 4 kV
1.1
DC Characteristics
†Notice: Stresses above those listed under “Maximum ratings” may cause permanent damage to the device. This is
a stress rating only and functional operation of the device at those or any other conditions above those indicated in
the operational listings of this specification is not implied. Exposure to maximum rating conditions for extended
periods may affect device reliability.
DS CHARACTERISTICS
Vcc = +2.5V to 5.5V
Industrial (I): T
AMB
= -40°C to +85°C
Param.
No.
Sym
Characteristic
Min.
Max.
Units
Test Conditions
SCL and SDA pins:
D1
V
IH
High-level input voltage
0.7 V
CC
—
V
D2
V
IL
Low-level input voltage
—
0.3 V
CC
V
Input levels on VCLK pin:
D3
V
IH
High-level input voltage
2.0
—
V
V
CC
≥ 2.7V (Note)
D4
V
IL
Low-level input voltage
—
0.2 V
CC
V
V
CC
≤ 2.7V (Note)
D5
V
HYS
Hysteresis of Schmitt trigger
Inputs
.05 V
CC
—
V
(Note)
D6
V
OL
1
Low-level output voltage
—
0.4
V
I
OL
= 3 mA, V
CC
= 2.5V (Note)
D7
V
OL
2
Low-level output voltage
—
0.6
V
I
OL
= 6 mA, V
CC
= 2.5V
D8
I
LI
Input leakage current
-10
10
µA
V
IN
= V
SS
or V
CC
D9
I
LO
Output leakage current
-10
10
µA
V
OUT
= V
SS
or V
CC
D10
C
IN
, C
OUT
Pin capacitance
(all inputs/outputs)
—
10
pF
V
CC
= 5.0V (Note)
T
AMB
= 25°C, F
CLK
= 1 MHz
Operating current:
D10
I
CC
W
RITE
Operating current
—
3
mA
V
CC
= 5.5V,
D11
I
CC
R
EAD
Operating current
—
1
mA
V
CC
= 5.5V, SCL = 400 kHz
D12
I
CCS
Standby current
—
—
30
100
µA
µA
V
CC
= 3.0V, SDA = SCL = V
CC
V
CC
= 5.5V, SDA = SCL = V
CC
V
CLK
= V
SS
Note:
This parameter is periodically sampled and not 100% tested.
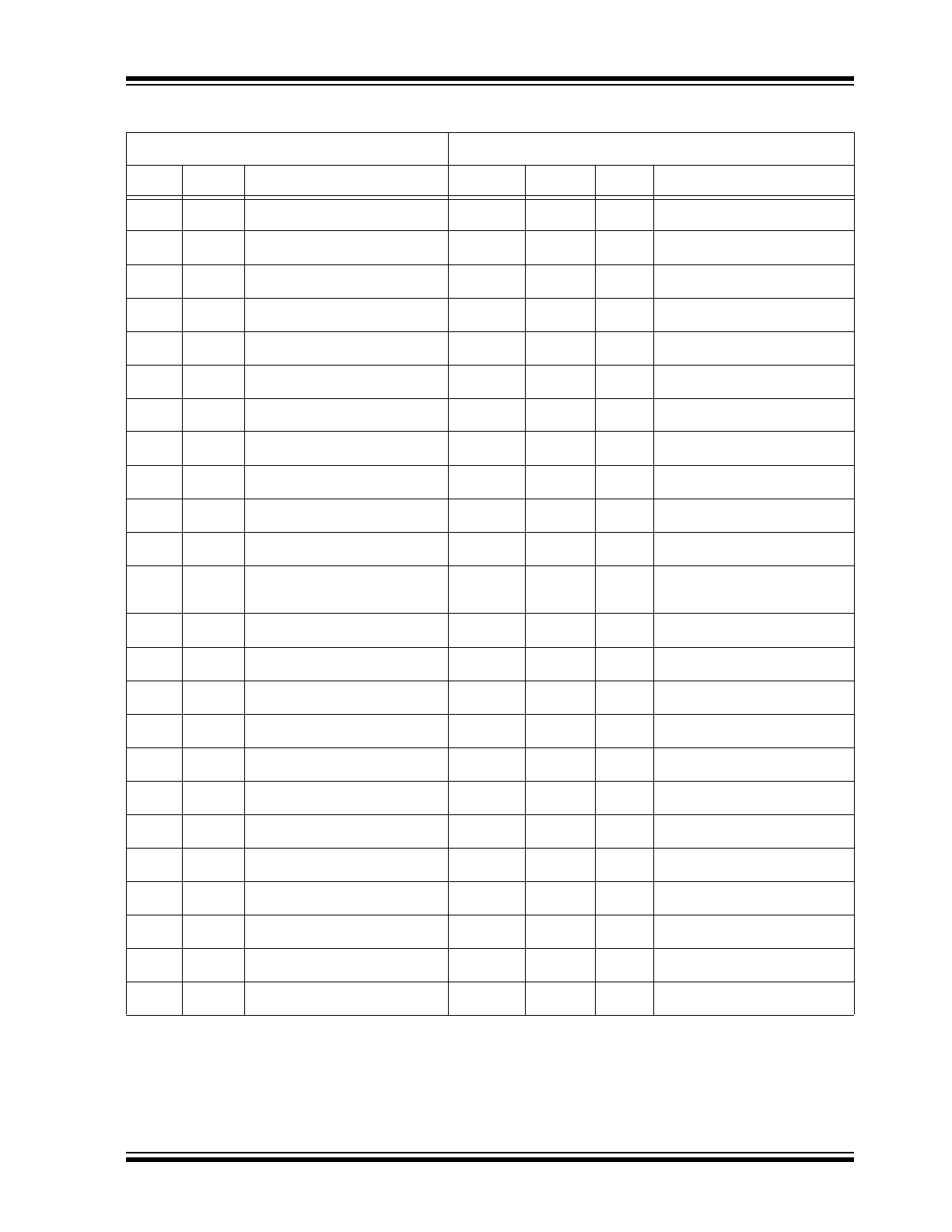
© 2007 Microchip Technology Inc.
DS21683B-page 3
24LC22A
1.2
AC Characteristics
AC CHARACTERISTICS
Vcc = +2.5V to 5.5V
Industrial (I):
T
AMB
= -40°C to +85°C
Param.
No.
Sym.
Parameter
Min.
Max.
Units
Conditions
1
F
CLK
Clock frequency
—
—
100
400
kHz
2.5V
≤ V
CC
≤ 5.5V
4.5V
≤ V
CC
≤ 5.5V
2
T
HIGH
Clock high time
4000
600
—
—
ns
2.5V
≤ V
CC
≤ 5.5V
4.5V
≤ V
CC
≤ 5.5V
3
T
LOW
Clock low time
4700
1300
—
—
ns
2.5V
≤ V
CC
≤ 5.5V
4.5V
≤ V
CC
≤ 5.5V
4
T
R
SDA and SCL rise time
—
—
1000
300
ns
2.5V
≤ V
CC
≤ 5.5V (Note 1)
4.5V
≤ V
CC
≤ 5.5V (Note 1)
5
T
F
SDA and SCL fall time
—
—
300
300
ns
(Note 1)
6
T
HD
:
STA
Start condition hold time
4000
600
—
—
ns
2.5V
≤ V
CC
≤ 5.5V
4.5V
≤ V
CC
≤ 5.5V
7
T
SU
:
STA
Start condition setup time
4700
600
—
—
ns
2.5V
≤ V
CC
≤ 5.5V
4.5V
≤ V
CC
≤ 5.5V
8
T
HD
:
DAT
Data input hold time
0
0
—
—
ns
(Note 2)
9
T
SU
:
DAT
Data input setup time
250
100
—
—
ns
2.5V
≤ V
CC
≤ 5.5V
4.5V
≤ V
CC
≤ 5.5V
10
T
SU
:
STO
Stop condition setup time
4000
600
—
—
ns
2.5V
≤ V
CC
≤ 5.5V
4.5V
≤ V
CC
≤ 5.5V
11
T
AA
Output valid from clock
(Note 2)
—
—
3500
900
ns
2.5V
≤ V
CC
≤ 5.5V
4.5V
≤ V
CC
≤ 5.5V
12
T
BUF
Bus free time: Time the bus must be
free before a new transmission can
start
4700
1300
—
—
ns
2.5V
≤ V
CC
≤ 5.5V
4.5V
≤ V
CC
≤ 5.5V
13
T
OF
Output fall time from V
IH
minimum to V
IL
maximum
—
20+0.1C
B
250
250
ns
2.5V
≤ V
CC
≤ 5.5V (Note 1)
4.5V
≤ V
CC
≤ 5.5V (Note 1)
14
T
SP
Input filter spike suppression
(SDA and SCL pins)
—
—
50
50
ns
(Notes 1 and 3)
15
T
WR
Write cycle time (byte or page)
—
—
10
10
ms
16
T
VAA
Output valid from VCLK
—
—
2000
1000
ns
17
T
VHIGH
VCLK high time
4000
600
—
—
ns
18
T
VLOW
VCLK low time
4700
1300
—
—
ns
19
T
VHST
VCLK setup time
0
0
—
—
ns
20
T
SPVL
VCLK hold time
4000
600
—
—
ns
21
T
VHZ
Mode transition time
—
—
1000
500
ns
22
T
VPU
Transmit-Only power up time
0
0
—
—
ns
23
T
SPV
Input filter spike suppression (VCLK
pin)
—
—
100
100
ns
24
—
Endurance
1M
—
cycles
25°C, V
CC
= 5.0V, Block mode
(Note 4)
Note
1: Not 100% tested. C
B
= total capacitance of one bus line in pF.
2: As a transmitter, the device must provide an internal minimum delay time to bridge the undefined region (minimum 300 ns) of
the falling edge of SCL to avoid unintended generation of Start or Stop conditions.
3: The combined T
SP
and V
HYS
specifications are due to Schmitt Trigger inputs which provide improved noise spike suppression.
This eliminates the need for a TI specification for standard operation.
4: This parameter is not tested but established by characterization. For endurance estimates in a specific application, please
consult the Total Endurance™ Model which can be obtained from Microchip’s web site at www.microchip.com.
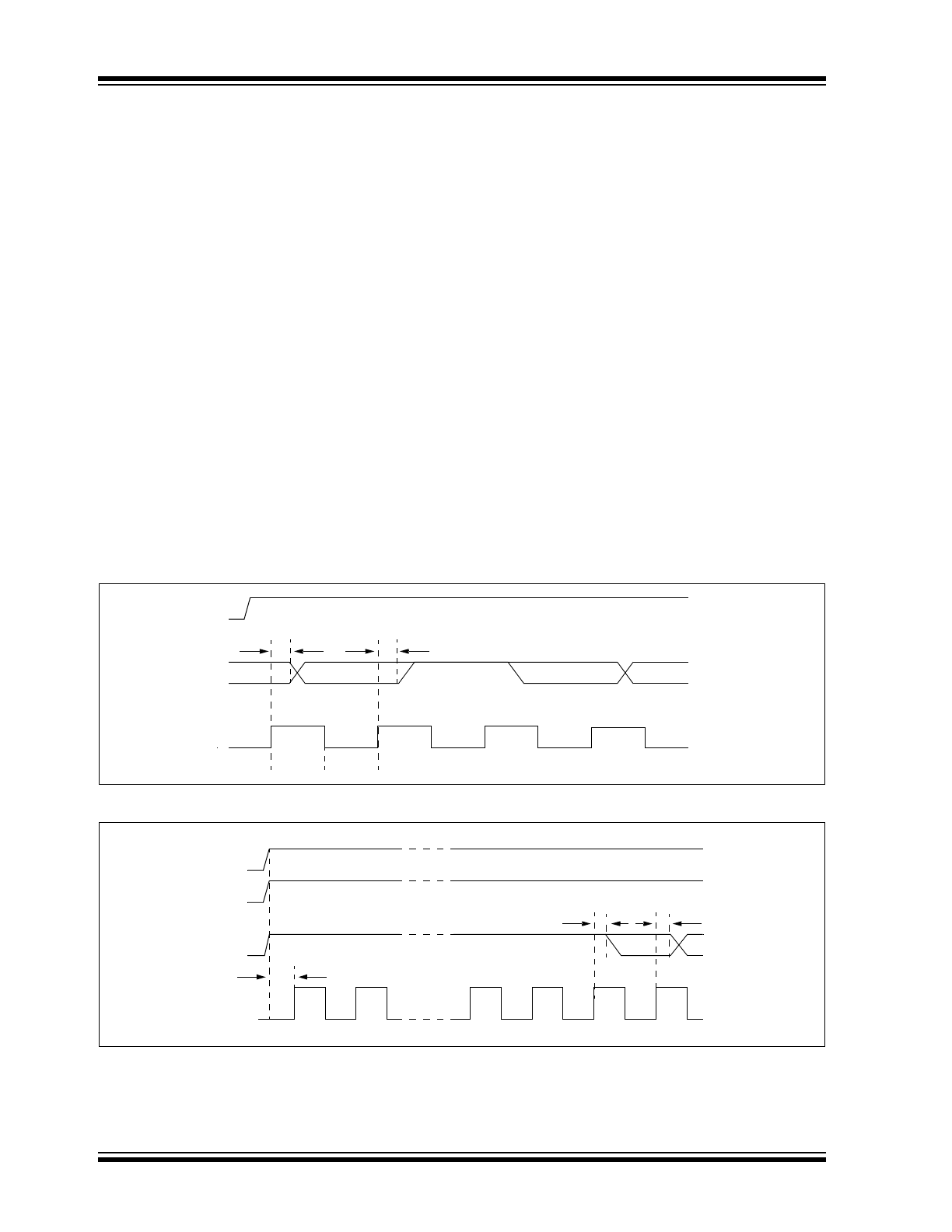
24LC22A
DS21683B-page 4
© 2007 Microchip Technology Inc.
2.0
FUNCTIONAL DESCRIPTION
The 24LC22A is designed to comply to the DDC Stan-
dard proposed by VESA (Figure 3-3) with the exception
that it is not Access.bus capable. It operates in two
modes, the Transmit-Only mode (1 Kbit) and the
Bidirectional mode (2 Kbit). There is a separate 2-wire
protocol to support each mode, each having a separate
clock input but sharing a common data line (SDA). The
device enters the Transmit-Only mode upon power-up.
In this mode, the device transmits data bits on the SDA
pin in response to a clock signal on the VCLK pin. The
device will remain in this mode until a valid high-to-low
transition is placed on the SCL input. When a valid tran-
sition on SCL is recognized, the device will switch into
the Bidirectional mode and look for its control byte to be
sent by the master. If it detects its control byte, it will
stay in the Bidirectional mode. Otherwise, it will revert
to the Transmit-Only mode after it sees 128 VCLK
pulses.
2.1
Transmit-Only Mode
The device will power-up in the Transmit-Only mode at
address 00h. This mode supports a unidirectional
2-wire protocol for continuous transmission of the first
1 Kbit of the memory array. This device requires that it
be initialized prior to valid data being sent in the Trans-
mit-Only mode (Section 2.2). In this mode, data is
transmitted on the SDA pin in 8-bit bytes, with each
byte followed by a ninth, Null bit (Figure 2-1). The clock
source for the Transmit-Only mode is provided on the
VCLK pin, and a data bit is output on the rising edge on
this pin. The eight bits in each byte are transmitted
Most Significant bit first. Each byte within the memory
array will be output in sequence. After address 7Fh in
the memory array is transmitted, the internal Address
Pointers will wrap-around to the first memory location
(00h) and continue. The Bidirectional mode Clock
(SCL) pin must be held high for the device to remain in
the Transmit-Only mode.
2.2
Initialization Procedure
After V
CC
has stabilized, the device will be in the
Transmit-Only mode. Nine clock cycles on the VCLK
pin must be given to the device for it to perform internal
sychronization. During this period, the SDA pin will be
in a high-impedance state. On the rising edge of the
tenth clock cycle, the device will output the first valid
data bit which will be the Most Significant bit in address
00h. (Figure 2-2).
FIGURE 2-1:
TRANSMIT-ONLY MODE
FIGURE 2-2:
DEVICE INITIALIZATION
SCL
SDA
VCLK
T
VAA
T
VAA
Bit 1 (LSB)
Null Bit
Bit 1 (MSB)
Bit 7
T
VLOW
T
VHIGH
T
VAA
T
VAA
Bit 8
Bit 7
High-Impedance for 9 Clock Cycles
T
VPU
1
2
8
9
10
11
SCL
SDA
VCLK
Vcc
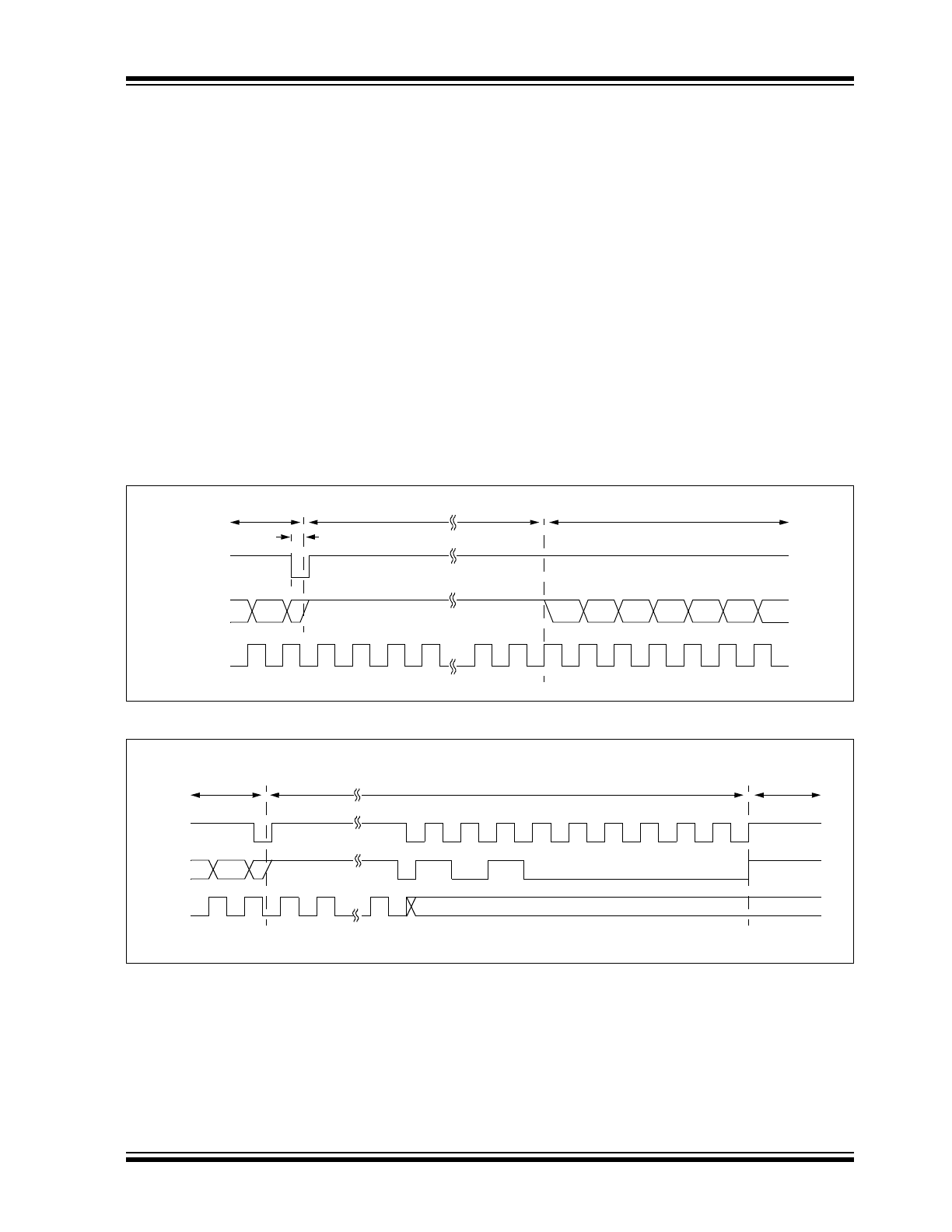
© 2007 Microchip Technology Inc.
DS21683B-page 5
24LC22A
3.0
BIDIRECTIONAL MODE
Before the 24LC22A can be switched into the Bidirec-
tional mode (Figure 3-1), it must enter the Transition
mode, which is done by applying a valid high-to-low
transition on the Bidirectional mode clock (SCL). As
soon it enters the Transition mode, it looks for a control
byte ‘1010 000X’ on the I
2
C™ bus, and starts to
count pulses on VCLK. Any high-to-low transition on
the SCL line will reset the count. If it sees a pulse count
of 128 on VCLK while the SCL line is idle, it will revert
back to the Transmit-Only mode, and transmit its con-
tents starting with the Most Significant bit in address
00h. However, if it detects the control byte on the I
2
C
bus, (Figure 3-2) it will switch to the in the Bidirectional
mode. Once the device has made the transition to the
Bidirectional mode, the only way to switch the device
back to the Transmit-Only mode is to remove power
from the device. The mode transition process is shown
in detail in Figure 3-3.
Once the device has switched into the Bidirectional
mode, the VCLK input is disregarded, with the excep-
tion that a logic high level is required to enable write
capability. In Bidirectional mode the user has access to
the entire 2K array, whereas in the Transmit-Only mode
the user can only access the first 1K. This mode sup-
ports a two-wire Bidirectional data transmission proto-
col (I
2
C). In this protocol, a device that sends data on
the bus is defined to be the transmitter, and a device
that receives data from the bus is defined to be the
receiver. The bus must be controlled by a master
device that generates the Bidirectional mode clock
(SCL), controls access to the bus and generates the
Start and Stop conditions, while the 24LC22A acts as
the slave. Both master and slave can operate as trans-
mitter or receiver, but the master device determines
which mode is activated. In the Bidirectional mode, the
24LC22A only responds to commands for device
‘1010 000X’.
FIGURE 3-1:
MODE TRANSITION WITH RECOVERY TO TRANSMIT-ONLY MODE
FIGURE 3-2:
SUCCESSFUL MODE TRANSITION TO BIDIRECTIONAL MODE
T
VHZ
SCL
SDA
VCLK
Transmit-Only
MODE
Bidirectional
Recovery to Transmit-Only mode
Bit 8
(MSB of data in 00h)
VCLK count =
1 2 3 4 127 128
Transition mode with possibility to return to Transmit-Only mode
Bidirectional
permanently
SCL
SDA
VCLK count = 1 2 n 0
VCLK
Transmit-Only
MODE
S
1
0
1
0
0
0
0
0
ACK
n < 128
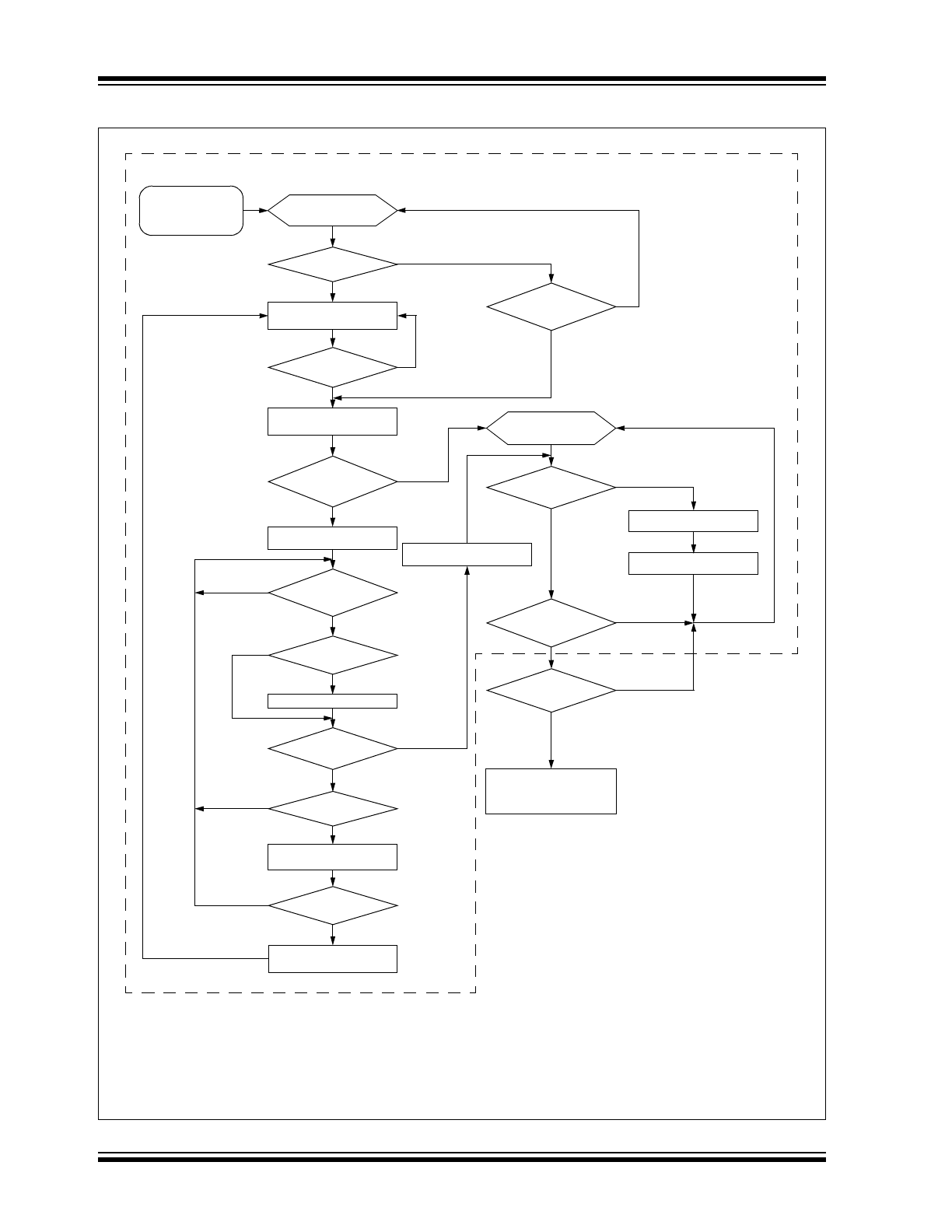
24LC22A
DS21683B-page 6
© 2007 Microchip Technology Inc.
FIGURE 3-3:
DISPLAY OPERATION PER DDC
STANDARD PROPOSED BY VESA
®
Communication
is idle
Is Vsync
present?
No
Send EDID continuously
using Vsync as clock
High-to-Low
transition on
SCL?
No
Yes
Yes
Stop sending EDID.
Switch to DDC2™ mode.
Display has
transition state
?
optional
Set Vsync counter = 0
Change on
VCLK lines?
SCL, SDA or
No
Yes
High-low
transition on SCL
?
Reset Vsync counter = 0
No
Yes
Valid
received?
DDC2 address
No
No
VCLK
cycle?
Yes
Increment VCLK counter
Yes
Switch back to DDC1™
mode.
DDC2 communication
idle. Display waiting for
address byte.
DDC2B
address
received?
Yes
Receive DDC2B
command
Respond to DDC2B
command
Is display
Access.busTM
Yes
Valid Access.bus
address?
No
Yes
See Access.bus
specification to determine
correct procedure.
Yes
No
Yes
No
No
No
The 24LC22A was designed to
Display Power-on
or
DDC Circuit Powered
from +5 volts
or start timer
Reset counter or timer
(if appropriate)
Counter=128 or
timer expired?
High-to-Low
transition on
SCL?
No
Yes
comply to the portion of flowchart inside dash box.
Note 1: The base flowchart is copyright
© 1993, 1994, 1995 Video Electronic Standard Association (VESA) from
VESA’s Display Data Channel (DDC) Standard Proposal ver. 2p rev. 0, used by permission of VESA.
2: The dash box and text “The 24LC21A and... inside dash box.” are added by Microchip Technology Inc.
3: Vsync signal is normally used to derive a signal for VCLK pin on the 24LCS22A.
capable?
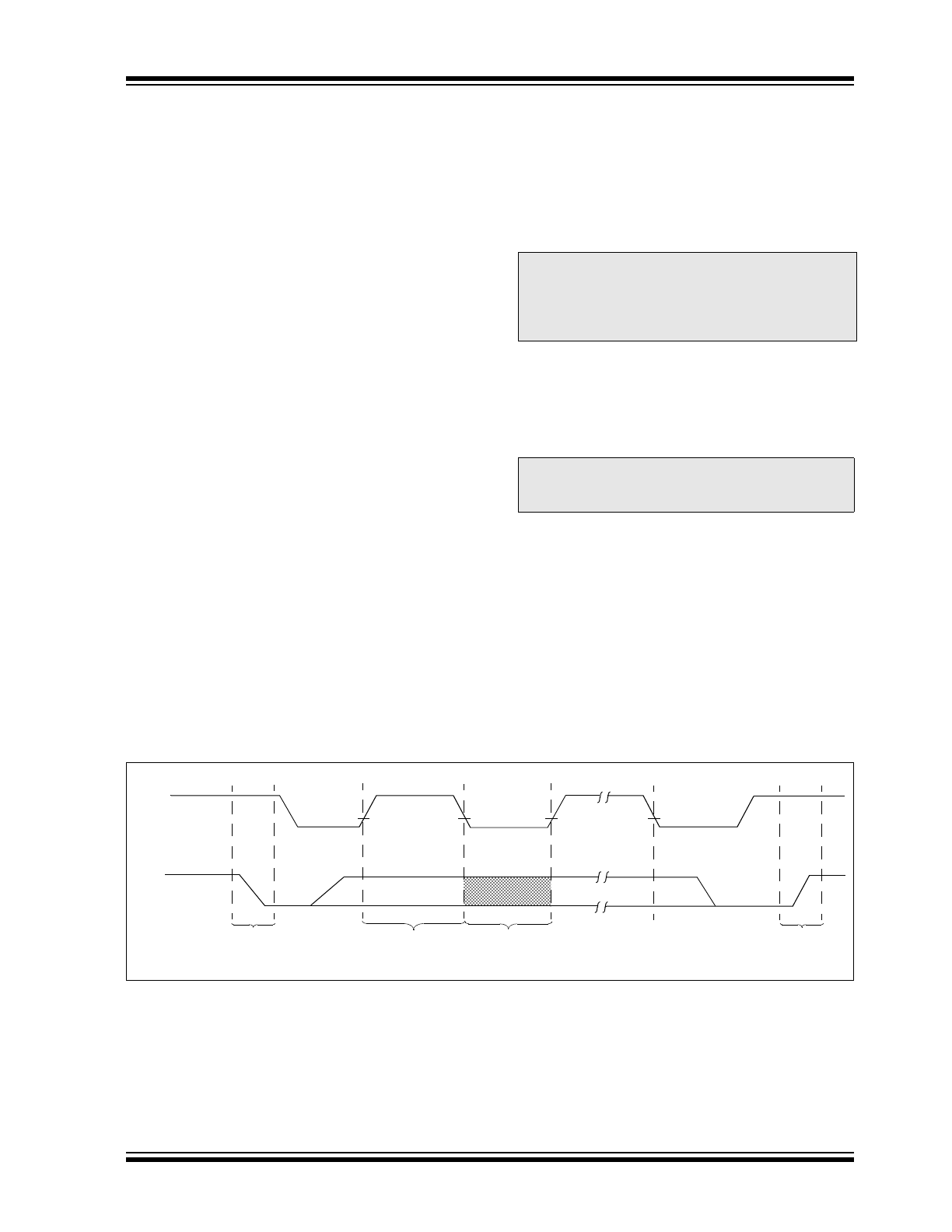
© 2007 Microchip Technology Inc.
DS21683B-page 7
24LC22A
3.1
Bidirectional Mode Bus
Characteristics
The following bus protocol has been defined:
• Data transfer may be initiated only when the bus
is not busy.
• During data transfer, the data line must remain
stable whenever the clock line is high. Changes in
the data line while the clock line is high will be
interpreted as a Start or Stop condition.
Accordingly, the following bus conditions have been
defined (Figure 3-4).
3.1.1
BUS NOT BUSY (A)
Both data and clock lines remain high.
3.1.2
START DATA TRANSFER (B)
A high-to-low transition of the SDA line while the clock
(SCL) is high determines a Start condition. All
commands must be preceded by a Start condition.
3.1.3
STOP DATA TRANSFER (C)
A low-to-high transition of the SDA line while the clock
(SCL) is high determines a Stop condition. All
operations must be ended with a Stop condition.
3.1.4
DATA VALID (D)
The state of the data line represents valid data when,
after a Start condition, the data line is stable for the
duration of the high period of the clock signal.
The data on the line must be changed during the low
period of the clock signal. There is one clock pulse per
bit of data.
Each data transfer is initiated with a Start condition and
terminated with a Stop condition. The number of the
data bytes transferred between the Start and Stop
conditions is determined by the master device and is
theoretically unlimited, although only the last eight will
be stored when doing a write operation. When an
overwrite does occur it will replace data in a first-in first-
out (FIFO) fashion.
3.1.5
ACKNOWLEDGE
Each receiving device, when addressed, is obliged to
generate an Acknowledge after the reception of each
byte. The master device must generate an extra clock
pulse which is associated with this Acknowledge bit.
The device that acknowledges has to pull down the
SDA line during the Acknowledge clock pulse in such a
way that the SDA line is stable low during the high
period of the acknowledge related clock pulse. Of
course, setup and hold times must be taken into
account. A master must signal an end of data to the
slave by not generating an acknowledge bit on the last
byte that has been clocked out of the slave. In this
case, the slave must leave the data line high to enable
the master to generate the Stop condition.
FIGURE 3-4:
DATA TRANSFER SEQUENCE ON THE SERIAL BUS
Note:
Once switched into Bidirectional mode, the
24LC22A will remain in that mode until
power is removed. Removing power is the
only way to reset the 24LC22A into the
Transmit-Only mode.
Note:
The 24LC22A does not generate any
Acknowledge bits if an internal
programming cycle is in progress.
(A)
(B)
(D)
(D)
(A)
(C)
Start
Condition
Address or
Acknowledge
Valid
Data
Allowed
to Change
Stop
Condition
SCL
SDA
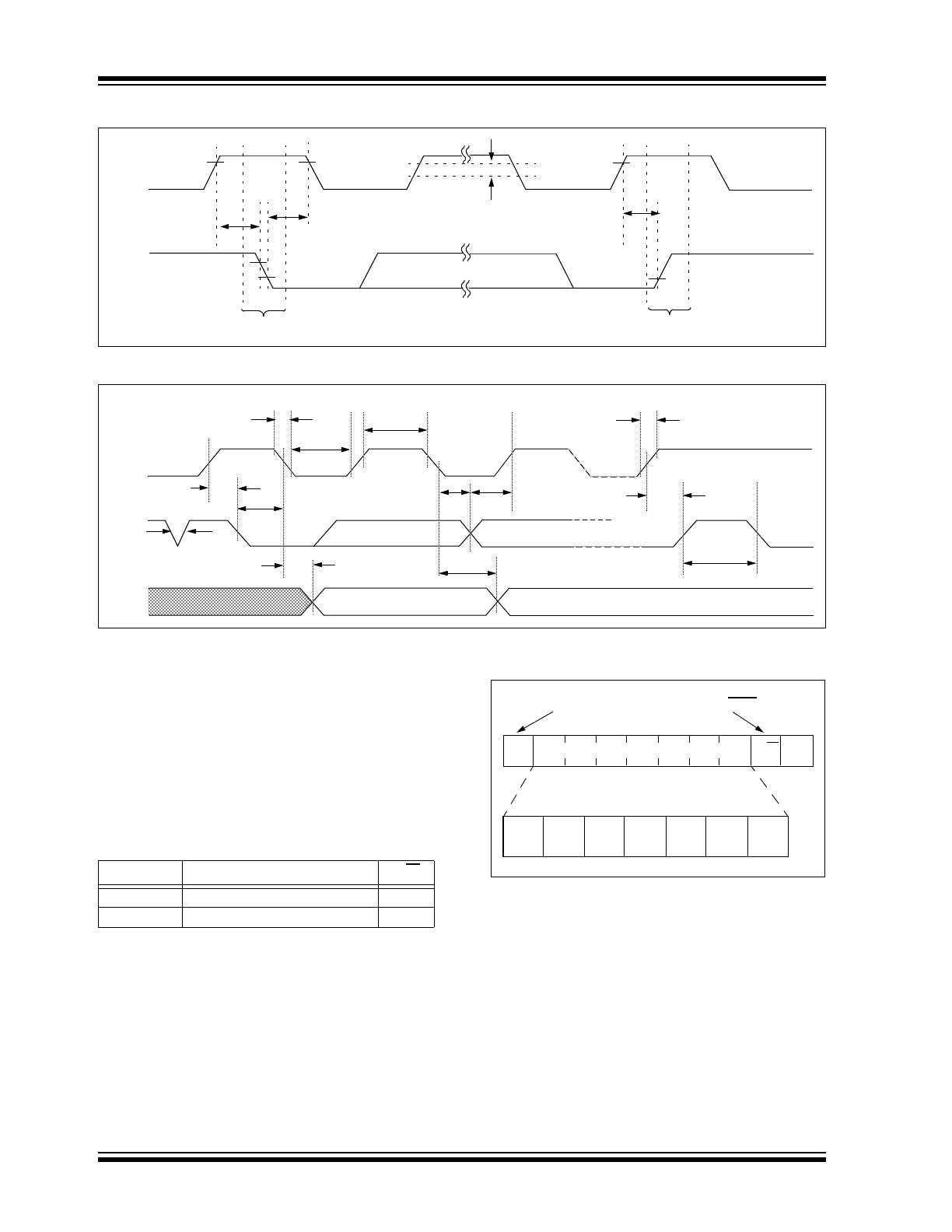
24LC22A
DS21683B-page 8
© 2007 Microchip Technology Inc.
FIGURE 3-5:
BUS TIMING START/STOP
FIGURE 3-6:
BUS TIMING DATA
3.1.6
SLAVE ADDRESS
After generating a Start condition, the bus master trans-
mits the slave address consisting of a 7-bit device code
(1010000) for the 24LC22A.
The eighth bit of slave address determines whether the
master device wants to read or write to the 24LC22A
(Figure 3-7).
The 24LC22A monitors the bus for its corresponding
slave address continuously. It generates an
Acknowledge bit if the slave address was true and it is
not in a programming mode.
FIGURE 3-7:
CONTROL BYTE
ALLOCATION
SCL
SDA
Start
Stop
V
HYS
T
SU
:
STO
T
HD
:
STA
T
SU
:
STA
SCL
SDA
IN
SDA
OUT
T
SU
:
STA
T
SP
T
AA
T
F
T
LOW
T
HIGH
T
HD
:
STA
T
HD
:
DAT
T
SU
:
DAT
T
SU
:
STO
T
BUF
T
AA
T
R
Operation
Slave Address
R/W
Read
1010000
1
Write
1010000
0
R/W A
1
0
1
0
0
0
0
Read/Write
Start
Slave Address
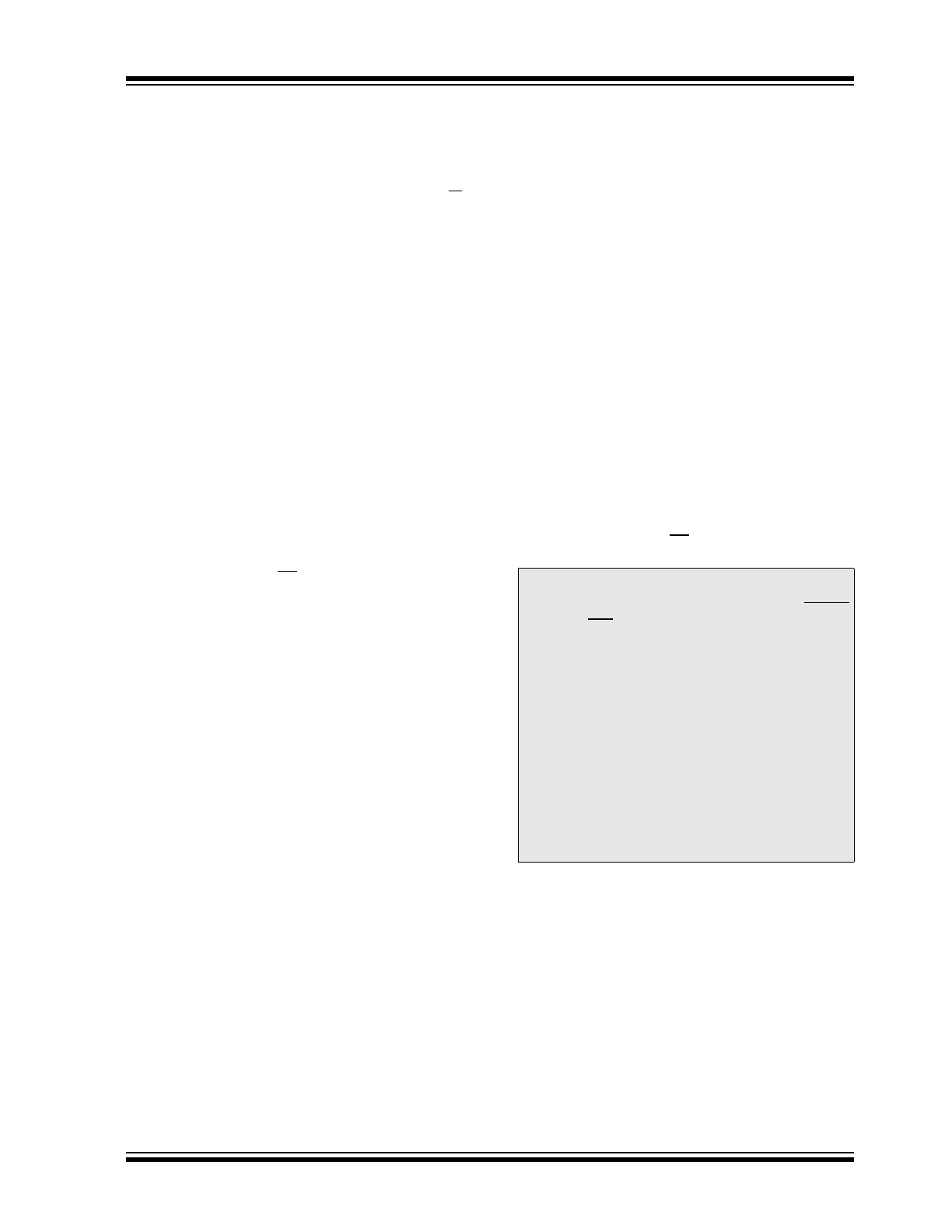
© 2007 Microchip Technology Inc.
DS21683B-page 9
24LC22A
4.0
WRITE OPERATION
4.1
Byte Write
Following the Start signal from the master, the slave
address (four bits), three zero bits (000) and the R/W
bit which is a logic low are placed onto the bus by the
master transmitter. This indicates to the addressed
slave receiver that a byte with a word address will
follow after it has generated an Acknowledge bit during
the ninth clock cycle. Therefore, the next byte
transmitted by the master is the word address and will
be written into the Address Pointer of the 24LC22A.
After receiving another Acknowledge signal from the
24LC22A the master device will transmit the data word
to be written into the addressed memory location. The
24LC22A acknowledges again and the master
generates a Stop condition. This initiates the internal
write cycle, and during this time the 24LC22A will not
generate Acknowledge signals (Figure 4-1).
It is required that VCLK be held at a logic high level
during command and data transfer in order to program
the device. This applies to both byte write and page
write operation. Note, however, that the VCLK is
ignored during the self-timed program operation.
Changing VCLK from high-to-low during the self-timed
program operation will not halt programming of the
device.
4.2
Page Write
The write control byte, word address and the first data
byte are transmitted to the 24LC22A in the same way
as in a byte write. But instead of generating a Stop
condition the master transmits up to eight data bytes to
the 24LC22A, which are temporarily stored in the on-
chip page buffer and will be written into the memory
after the master has transmitted a Stop condition. After
the receipt of each word, the three lower order Address
Pointer bits are internally incremented by one. The
higher order five bits of the word address remains
constant. If the master should transmit more than eight
words prior to generating the Stop condition, the
address counter will roll over and the previously
received data will be overwritten. As with the byte write
operation, once the Stop condition is received an
internal write cycle will begin (Figure 4-3).
It is required that VCLK be held at a logic high level
during command and data transfer in order to program
the device. This applies to both byte write and page
write operation. Note, however, that the VCLK is
ignored during the self-timed program operation.
Changing VCLK from high-to-low during the self-timed
program operation will not halt programming of the
device.
Note:
Page write operations are limited to writing
bytes within a single physical page, regard-
less of the number of bytes actually being
written. Physical page boundaries start at
addresses that are integer multiples of the
page buffer size (or ‘page size’) and end at
addresses that are integer multiples of
[page size – 1]. If a Page Write command
attempts to write across a physical page
boundary, the result is that the data wraps
around to the beginning of the current page
(overwriting data previously stored there),
instead of being written to the next page as
might be expected. It is therefore neces-
sary for the application software to prevent
page write operations that would attempt to
cross a page boundary.
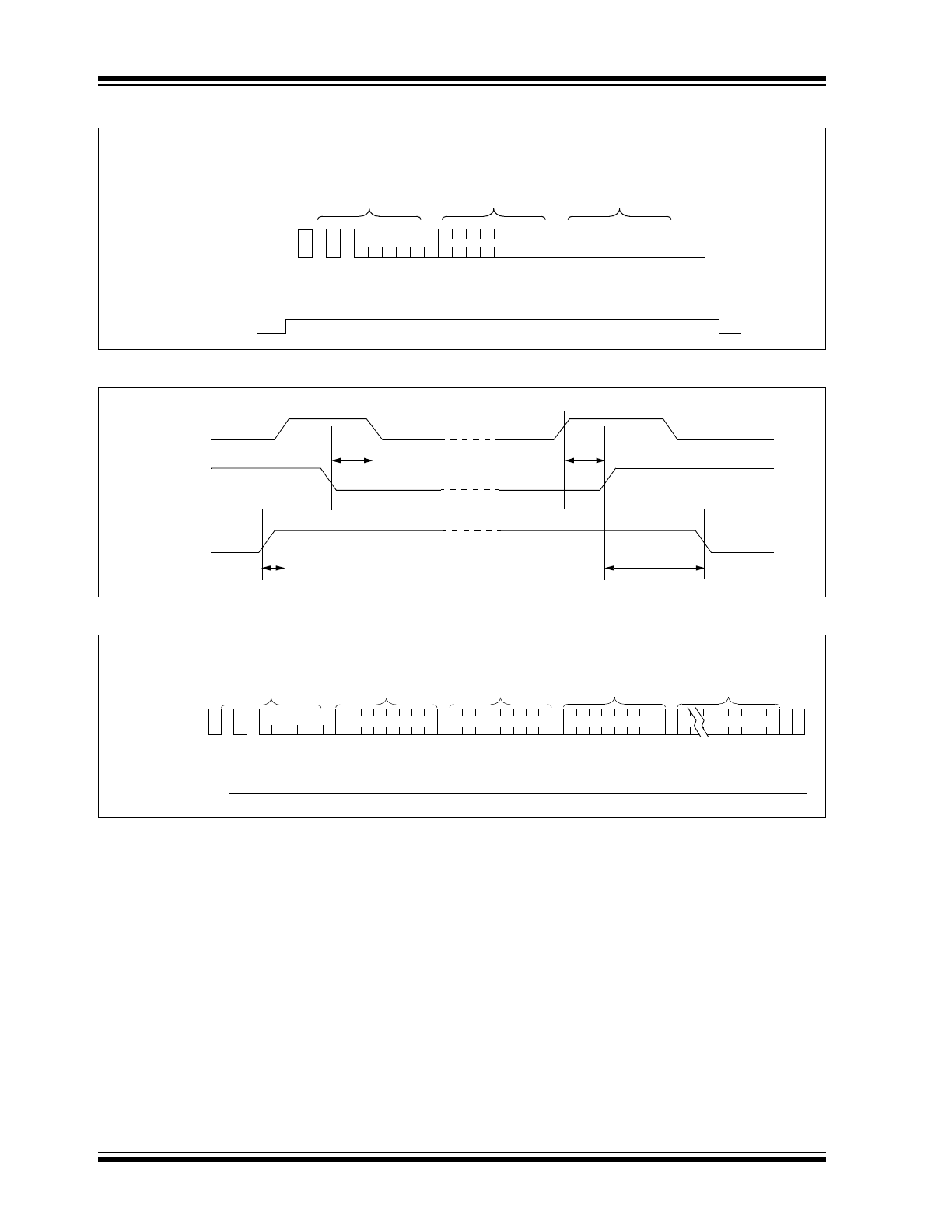
24LC22A
DS21683B-page 10
© 2007 Microchip Technology Inc.
FIGURE 4-1:
BYTE WRITE
FIGURE 4-2:
VCLK WRITE ENABLE TIMING
FIGURE 4-3:
PAGE WRITE
Bus Activity
Master
SDA Line
Bus Activity
Control
Byte
Word
Address
Data
S
T
O
P
S
T
A
R
T
A
C
K
S
P
A
C
K
A
C
K
VCLK
SCL
SDA
IN
VCLK
T
HD
:
STA
T
HD
:
STO
T
VHST
T
SPVL
SDA Line
Control
Byte
Word
Address
S
T
O
P
S
T
A
R
T
A
C
K
A
C
K
A
C
K
A
C
K
A
C
K
Data n + 1
Data n + 7
Data (n)
P
S
VCLK
Bus Activity
Master
Bus Activity