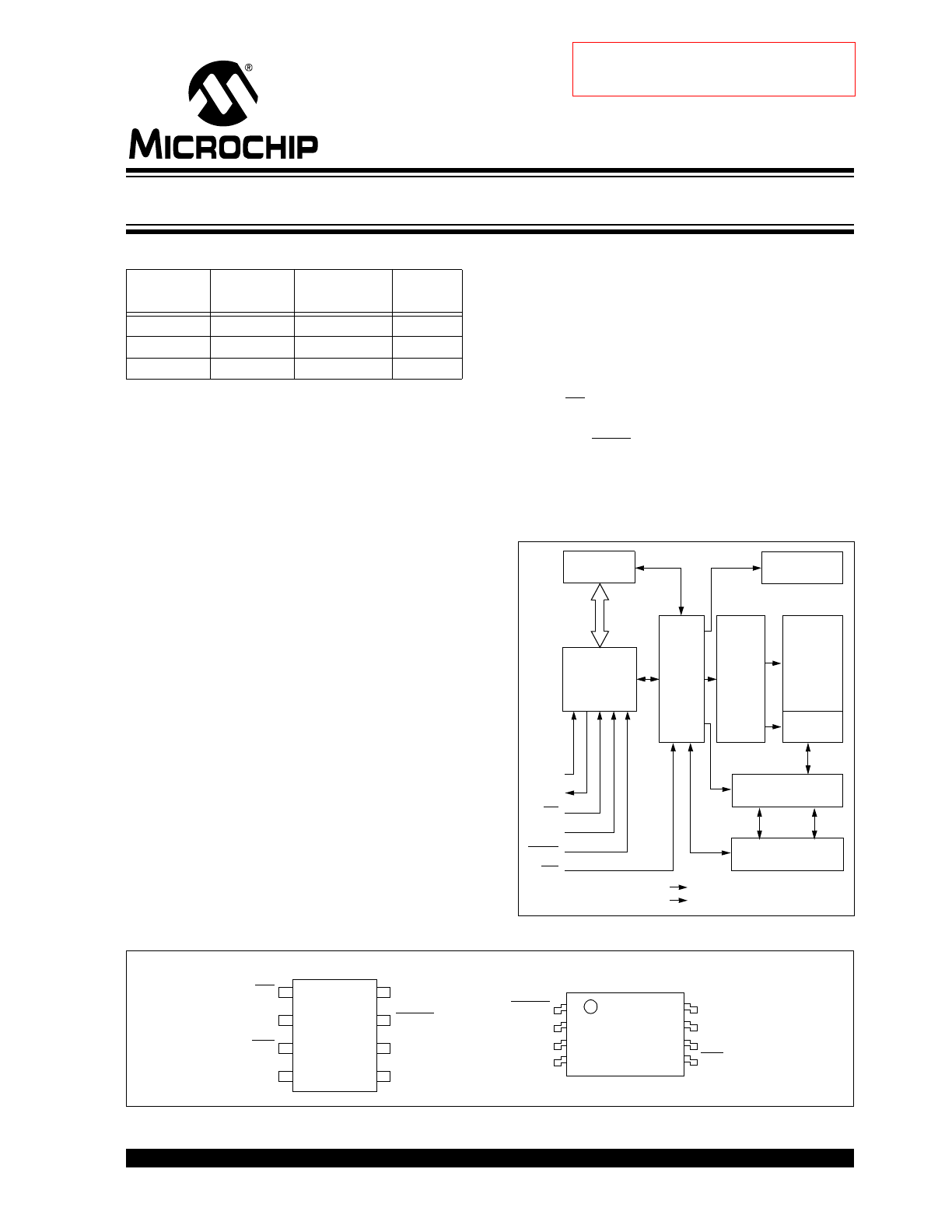
© 2008 Microchip Technology Inc.
DS21223H-page 1
25AA640/25LC640
Device Selection Table
Features:
• Low-Power CMOS Technology
- Write current: 3 mA, typical
- Read current: 500
μ
A, typical
- Standby current: 500 nA, typical
• 8192 x 8 Bit Organization
• 32 Byte Page
• Write Cycle Time: 5 ms max.
• Self-Timed Erase and Write Cycles
• Block Write Protection
- Protect none, 1/4, 1/2 or all of array
• Built-in Write Protection
- Power on/off data protection circuitry
- Write enable latch
- Write-protect pin
• Sequential Read
• High Reliability
- Data retention: > 200 years
- ESD protection: > 4000V
• 8-pin PDIP, SOIC and TSSOP Packages
• Temperature Ranges Supported:
- Industrial (I): -40
°C to +85°C
- Automotive (E): -40
°C to +125°C
Description:
The Microchip Technology Inc. 25AA640/25LC640
(25XX640
*
) is a 64 Kbit Serial Electrically Erasable
PROM [EEPROM]. The memory is accessed via a
simple Serial Peripheral Interface (SPI) compatible
serial bus. The bus signals required are a clock input
(SCK) plus separate data in (SI) and data out (SO)
lines. Access to the device is controlled through a Chip
Select (CS) input.
Communication to the device can be paused via the
hold pin (HOLD). While the device is paused,
transitions on its inputs will be ignored, with the
exception of Chip Select, allowing the host to service
higher priority interrupts.
Block Diagram
Package Types
Part
Number
V
CC
Range
Max Clock
Frequency
Temp
Ranges
25AA640
1.8-5.5V
1 MHz
I
25LC640
2.5-5.5V
2 MHz
I
25LC640
4.5-5.5V
3/2.5 MHz
I, E
SI
SO
SCK
CS
HOLD
WP
I/O Control
Memory
Control
Logic
HV Generator
EEPROM
Array
Page
Y Decoder
Sense Amp.
R/W Control
Logic
V
CC
V
SS
Latches
XDEC
STATUS
Register
25XX6
40
25
X
X
6
40
PDIP/SOIC
TSSOP
CS
SO
WP
V
SS
V
CC
HOLD
SCK
SI
8
7
6
5
1
2
3
4
8
7
6
5
1
2
3
4
HOLD
V
CC
CS
SO
SCK
SI
V
SS
WP
64K SPI Bus Serial EEPROM
*25XX640 is used in this document as a generic part number for the 25AA640/25LC640 devices.
Not recommended for new designs –
Please use 25AA640A or 25LC640A.

25AA640/25LC640
DS21223H-page 2
© 2008 Microchip Technology Inc.
1.0
ELECTRICAL CHARACTERISTICS
Absolute Maximum Ratings
(†)
V
CC
.............................................................................................................................................................................7.0V
All inputs and outputs w.r.t. V
SS
........................................................................................................ -0.6V to V
CC
+ 1.0V
Storage temperature .................................................................................................................................-65°C to 150°C
Ambient temperature under bias ...............................................................................................................-65°C to 125°C
ESD protection on all pins .......................................................................................................................................... 4 kV
TABLE 1-1:
DC CHARACTERISTICS
† NOTICE: Stresses above those listed under “Absolute Maximum Ratings” may cause permanent damage to the
device. This is a stress rating only and functional operation of the device at those or any other conditions above those
indicated in the operational listings of this specification is not implied. Exposure to maximum rating conditions for an
extended period of time may affect device reliability.
DC CHARACTERISTICS
Industrial (I):
T
A
= -40°C to +85°C
V
CC
= 1.8V to 5.5V
Automotive (E): T
A
= -40°C to +125°C V
CC
= 4.5V to 5.5V
Param.
No.
Sym
Characteristics
Min
Max
Units
Conditions
D1
V
IH
1
High-level input
voltage
2.0
V
CC
+ 1
V
V
CC
≥ 2.7V (Note 1)
D2
V
IH
2
0.7 V
CC
V
CC
+ 1
V
V
CC
< 2.7V (Note 1)
D3
V
IL
1
Low-level input
voltage
-0.3
0.8
V
V
CC
≥ 2.7V (Note 1)
D4
V
IL
2
-0.3
0.2 V
CC
V
V
CC
< 2.7V (Note 1)
D5
V
OL
Low-level output
voltage
—
0.4
V
I
OL
= 2.1 mA
—
0.2
V
I
OL
= 1.0 mA, V
CC
= < 2.5V
D6
V
OH
High-level output
voltage
V
CC
- 0.5
—
V
I
OH
= -400
μA
D7
I
LI
Input leakage current
—
±1
μA
CS = V
CC
, V
IN
= V
SS
TO
V
CC
D8
I
LO
Output leakage
current
—
±1
μA
CS = V
CC
, V
OUT
= V
SS
TO
V
CC
D9
C
INT
Internal Capacitance
(all inputs and
outputs)
—
7
pF
T
A
= 25°C, CLK = 1.0 MHz,
V
CC
= 5.0V (Note 1)
D10
I
CC
Read Operating Current
—
—
1
500
mA
μA
V
CC
= 5.5V; F
CLK
= 3.0 MHz;
SO = Open
V
CC
= 2.5V; F
CLK
= 2.0 MHz;
SO = Open
D11
I
CC
Write
—
—
5
3
mA
mA
V
CC
= 5.5V
V
CC
= 2.5V
D12
I
CCS
Standby Current
—
—
5
1
μA
μA
CS = V
CC
= 5.5V, Inputs tied to V
CC
or
V
SS
CS = V
CC
= 2.5V, Inputs tied to V
CC
or
V
SS
Note 1:
This parameter is periodically sampled and not 100% tested.

© 2008 Microchip Technology Inc.
DS21223H-page 3
25AA640/25LC640
TABLE 1-2:
AC CHARACTERISTICS
AC CHARACTERISTICS
Industrial (I):
T
A
= -40°C to +85°C
V
CC
= 1.8V to 5.5V
Automotive (E): T
A
= -40°C to +125°C
V
CC
= 4.5V to 5.5V
Param.
No.
Sym
Characteristic
Min
Max
Units
Conditions
1
F
CLK
Clock Frequency
—
—
—
3
2
1
MHz
MHz
MHz
V
CC
= 4.5V to 5.5V (Note 2)
V
CC
= 2.5V to 5.5V
V
CC
= 1.8V to 5.5V
2
T
CSS
CS Setup Time
100
250
500
—
—
—
ns
ns
ns
V
CC
= 4.5V to 5.5V
V
CC
= 2.5V to 5.5V
V
CC
= 1.8V to 5.5V
3
T
CSH
CS Hold Time
150
250
475
—
—
—
ns
ns
ns
V
CC
= 4.5V to 5.5V
V
CC
= 2.5V to 5.5V
V
CC
= 1.8V to 5.5V
4
T
CSD
CS Disable Time
500
—
ns
5
T
SU
Data Setup Time
30
50
50
—
—
—
ns
ns
ns
V
CC
= 4.5V to 5.5V
V
CC
= 2.5V to 5.5V
V
CC
= 1.8V to 5.5V
6
T
HD
Data Hold Time
50
100
100
—
—
—
ns
ns
ns
V
CC
= 4.5V to 5.5V
V
CC
= 2.5V to 5.5V
V
CC
= 1.8V to 5.5V
7
T
R
CLK Rise Time
—
2
μs
(Note 1)
8
T
F
CLK Fall Time
—
2
μs
(Note 1)
9
T
HI
Clock High Time
150
230
475
—
—
—
ns
ns
ns
V
CC
= 4.5V to 5.5V
V
CC
= 2.5V to 5.5V
V
CC
= 1.8V to 5.5V
10
T
LO
Clock Low Time
150
230
475
—
—
—
ns
ns
ns
V
CC
= 4.5V to 5.5V
V
CC
= 2.5V to 5.5V
V
CC
= 1.8V to 5.5V
11
T
CLD
Clock Delay Time
50
—
ns
12
T
CLE
Clock Enable Time
50
—
ns
13
T
V
Output Valid from
Clock Low
—
—
—
150
230
475
ns
ns
ns
V
CC
= 4.5V to 5.5V
V
CC
= 2.5V to 5.5V
V
CC
= 1.8V to 5.5V
14
T
HO
Output Hold Time
0
—
ns
(Note 1)
15
T
DIS
Output Disable Time
—
—
—
200
250
500
ns
ns
ns
V
CC
= 4.5V to 5.5V (Note 1)
V
CC
= 2.5V to 5.5V (Note 1)
V
CC
= 1.8V to 5.5V (Note 1)
16
T
HS
HOLD Setup Time
100
100
200
—
—
—
ns
ns
ns
V
CC
= 4.5V to 5.5V
V
CC
= 2.5V to 5.5V
V
CC
= 1.8V to 5.5V
17
T
HH
HOLD Hold Time
100
100
200
—
—
—
ns
ns
ns
V
CC
= 4.5V to 5.5V
V
CC
= 2.5V to 5.5V
V
CC
= 1.8V to 5.5V
18
T
HZ
HOLD Low to Output
High-Z
100
150
200
—
—
—
ns
ns
ns
V
CC
= 4.5V to 5.5V (Note 1)
V
CC
= 2.5V to 5.5V (Note 1)
V
CC
= 1.8V to 5.5V (Note 1)
19
T
HV
HOLD High to Output
Valid
100
150
200
—
—
—
ns
ns
ns
V
CC
= 4.5V to 5.5V
V
CC
= 2.5V to 5.5V
V
CC
= 1.8V to 5.5V
20
T
WC
Internal Write Cycle
Time
—
5
ms
21
—
Endurance
1M
—
E/W
Cycles
(Note 3)
Note
1: This parameter is periodically sampled and not 100% tested.
2: F
CLK
max. = 2.5 MHz for T
A
> 85°C.
3: This parameter is not tested but established by characterization. For endurance estimates in a specific application,
please consult the Total Endurance™ Model which can be obtained from Microchip’s web site at: www.microchip.com.
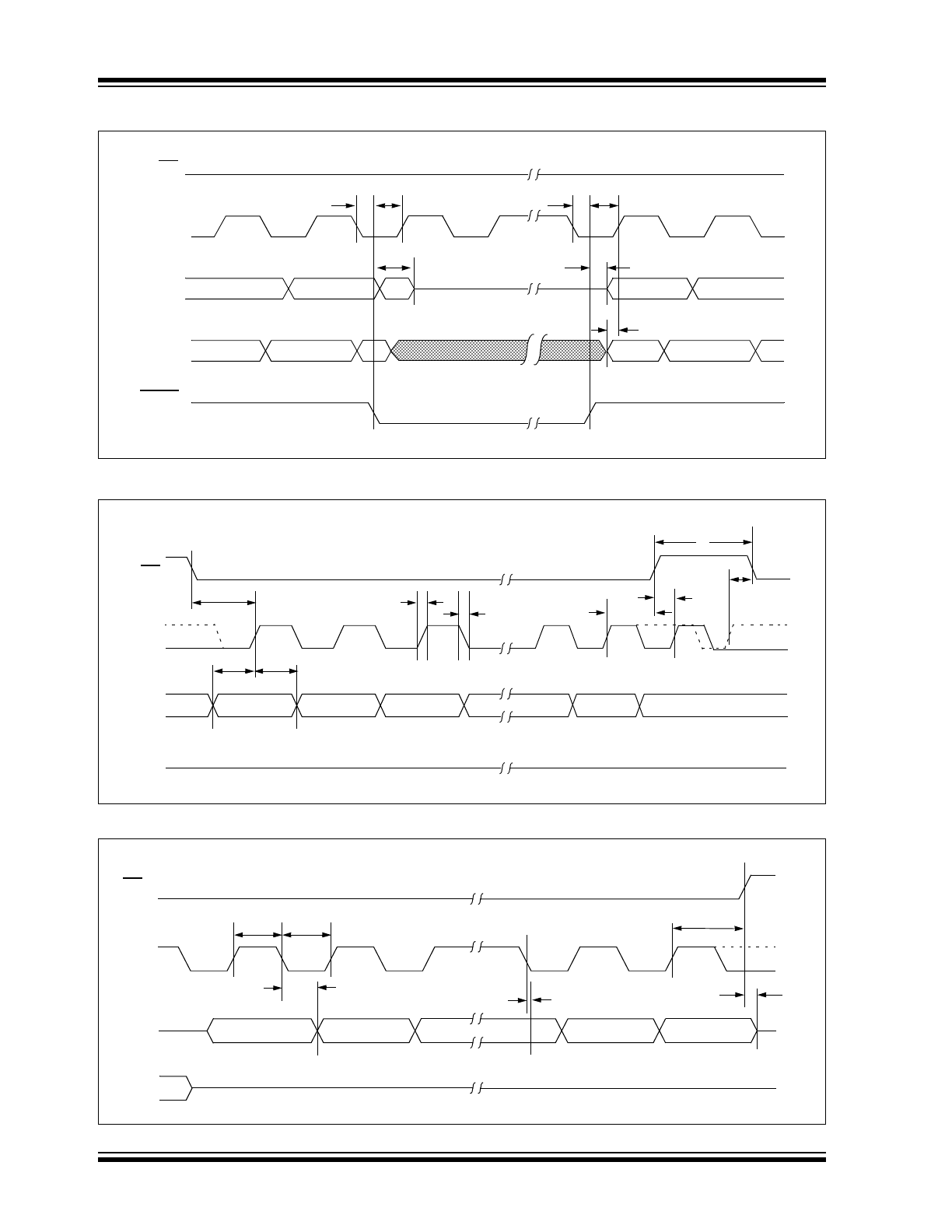
25AA640/25LC640
DS21223H-page 4
© 2008 Microchip Technology Inc.
FIGURE 1-1:
HOLD TIMING
FIGURE 1-2:
SERIAL INPUT TIMING
FIGURE 1-3:
SERIAL OUTPUT TIMING
CS
SCK
SO
SI
HOLD
17
16
16
17
19
18
Don’t Care
5
High-Impedance
n + 2
n + 1
n
n - 1
n
n + 2
n + 1
n
n
n - 1
CS
SCK
SI
SO
6
5
8
7
11
3
LSB In
MSB In
High-Impedance
12
Mode 1,1
Mode 0,0
4
2
CS
SCK
SO
10
9
13
MSB Out
LSB Out
3
15
Don’t Care
SI
Mode 1,1
Mode 0,0
14
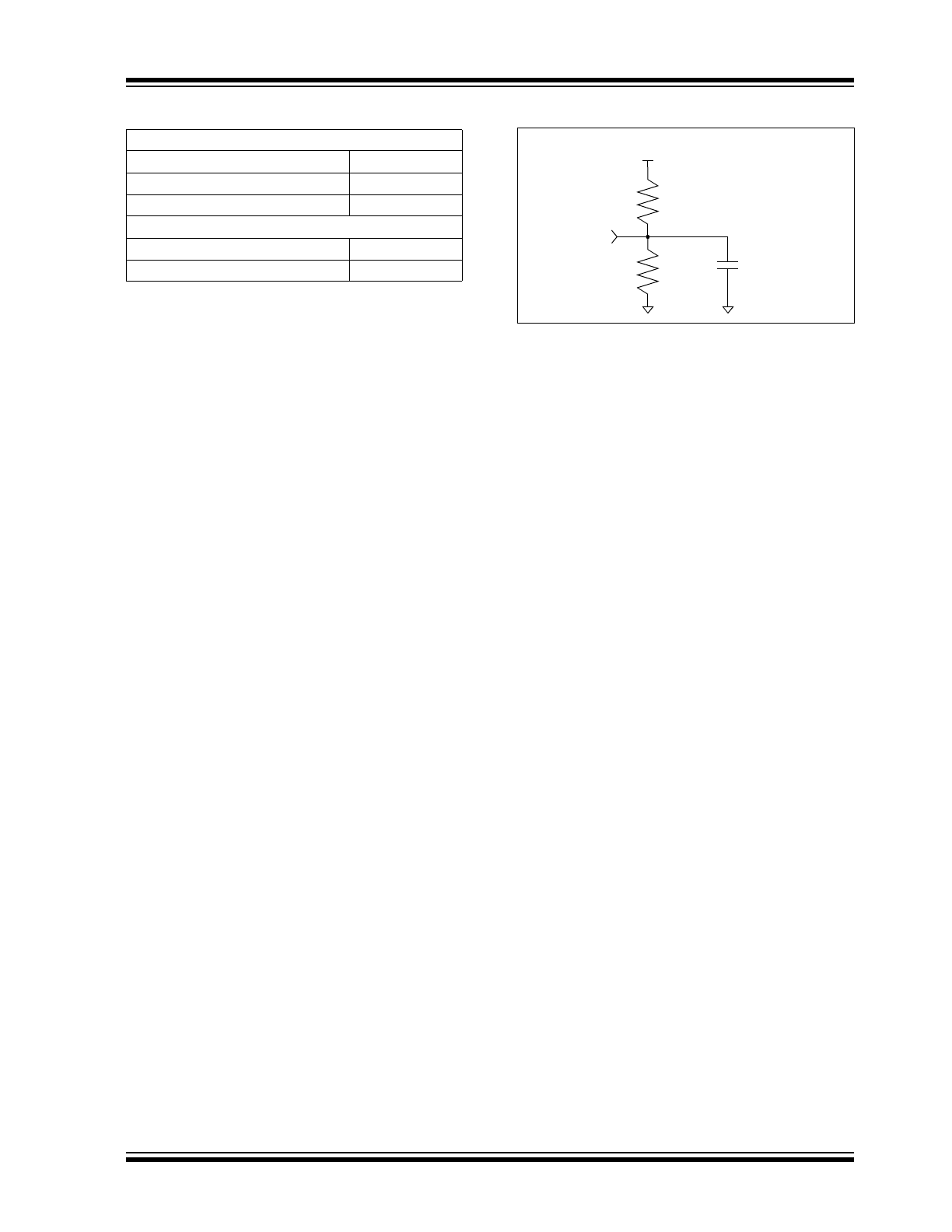
© 2008 Microchip Technology Inc.
DS21223H-page 5
25AA640/25LC640
TABLE 1-3:
AC TEST CONDITIONS
FIGURE 1-4:
AC TEST CIRCUIT
AC Waveform:
V
LO
= 0.2V
V
H I
= V
CC
– 0.2V
(Note 1)
V
H I
= 4.0V
(Note 2)
Timing Measurement Reference Level
Input
0.5 V
CC
Output
0.5 V
CC
Note 1: For V
CC
≤ 4.0V
2: For V
CC
> 4.0V
V
CC
SO
100 pF
1.8 k
Ω
2.25 k
Ω
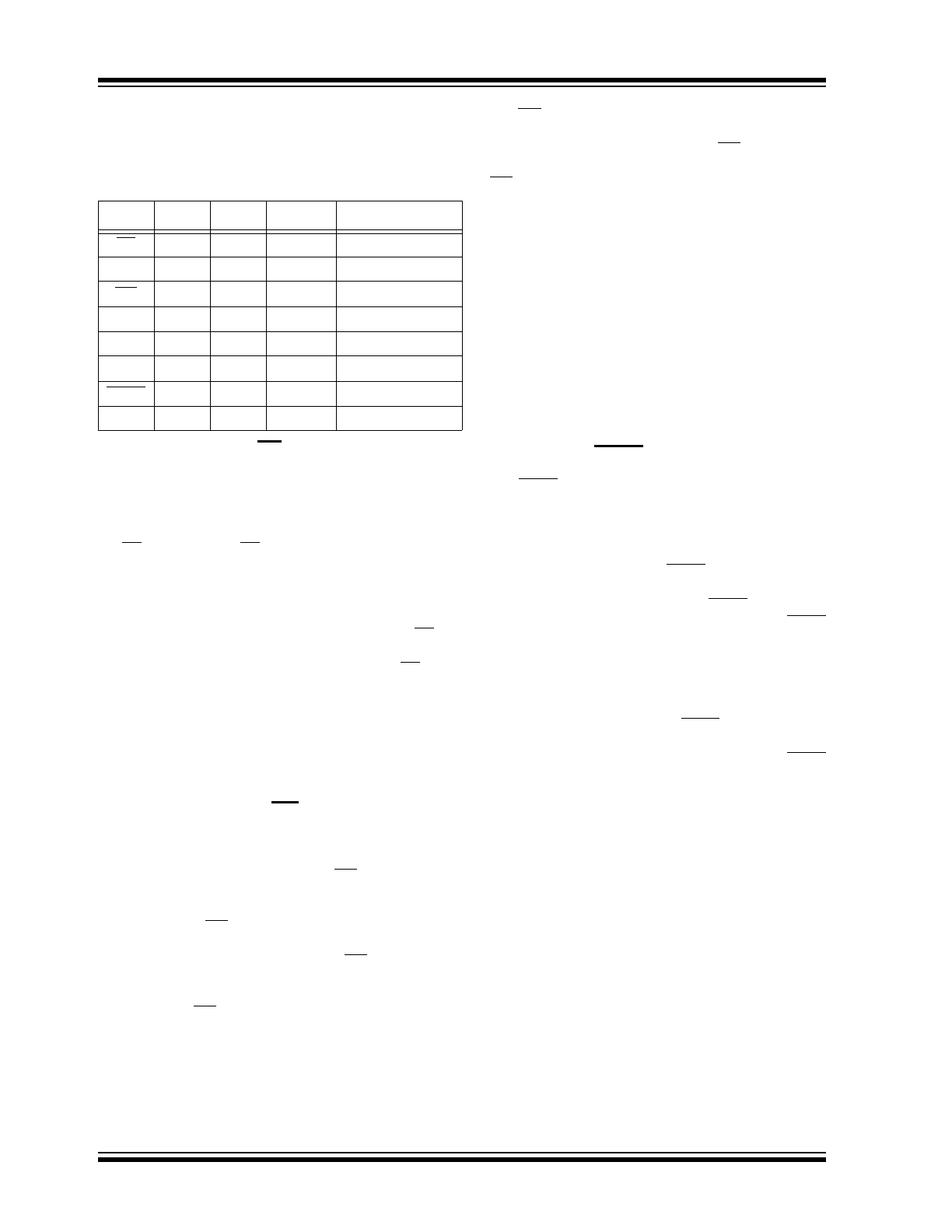
25AA640/25LC640
DS21223H-page 6
© 2008 Microchip Technology Inc.
2.0
PIN DESCRIPTIONS
The descriptions of the pins are listed in Table 2-1.
TABLE 2-1:
PIN FUNCTION TABLE
2.1
Chip Select (CS)
A low level on this pin selects the device. A high level
deselects the device and forces it into Standby mode.
However, a programming cycle which is already
initiated or in progress will be completed, regardless of
the CS input signal. If CS is brought high, or remains
high during a program cycle, the device will go into
Standby mode when the programming cycle is
complete. When the device is deselected, SO goes to
the high-impedance state, allowing multiple parts to
share the same SPI bus. A low-to-high transition on CS
after a valid write sequence initiates an internal write
cycle. After power-up, a high-to-low transition on CS is
required prior to any sequence being initiated.
2.2
Serial Output (SO)
The SO pin is used to transfer data out of the 25XX640.
During a read cycle, data is shifted out on this pin after
the falling edge of the serial clock.
2.3
Write-Protect (WP)
This pin is used in conjunction with the WPEN bit in the
STATUS register to prohibit writes to the nonvolatile
bits in the STATUS register. When WP is low and
WPEN is high, writing to the nonvolatile bits in the STA-
TUS register is disabled. All other operations function
normally. When WP is high, all functions, including
writes to the nonvolatile bits in the STATUS register
operate normally. If the WPEN bit is set, WP low during
a STATUS register write sequence will disable writing
to the STATUS register. If an internal write cycle has
already begun, WP going low will have no effect on the
write.
The WP pin function is blocked when the WPEN bit in
the STATUS register is low. This allows the user to
install the 25XX640 in a system with WP pin grounded
and still be able to write to the STATUS register. The
WP pin functions will be enabled when the WPEN bit is
set high.
2.4
Serial Input (SI)
The SI pin is used to transfer data into the device. It
receives instructions, addresses, and data. Data is
latched on the rising edge of the serial clock.
2.5
Serial Clock (SCK)
The SCK is used to synchronize the communication
between a master and the 25XX640. Instructions,
addresses, or data present on the SI pin are latched on
the rising edge of the clock input, while data on the SO
pin is updated after the falling edge of the clock input.
2.6
Hold (HOLD)
The HOLD pin is used to suspend transmission to the
25XX640 while in the middle of a serial sequence with-
out having to retransmit the entire sequence over
again. It must be held high any time this function is not
being used. Once the device is selected and a serial
sequence is underway, the HOLD pin may be pulled
low to pause further serial communication without
resetting the serial sequence. The HOLD pin must be
brought low while SCK is low, otherwise the HOLD
function will not be invoked until the next SCK high-to-
low transition. The 25XX640 must remain selected
during this sequence. The SI, SCK, and SO pins are in
a high-impedance state during the time the device is
paused and transitions on these pins will be ignored. To
resume serial communication, HOLD must be brought
high while the SCK pin is low, otherwise serial
communication will not resume. Lowering the HOLD
line at any time will tri-state the SO line.
Name
PDIP
SOIC
TSSOP
Description
CS
1
1
3
Chip Select Input
SO
2
2
4
Serial Data Output
WP
3
3
5
Write-Protect Pin
V
SS
4
4
6
Ground
SI
5
5
7
Serial Data Input
SCK
6
6
8
Serial Clock Input
HOLD
7
7
1
Hold Input
V
CC
8
8
2
Supply Voltage
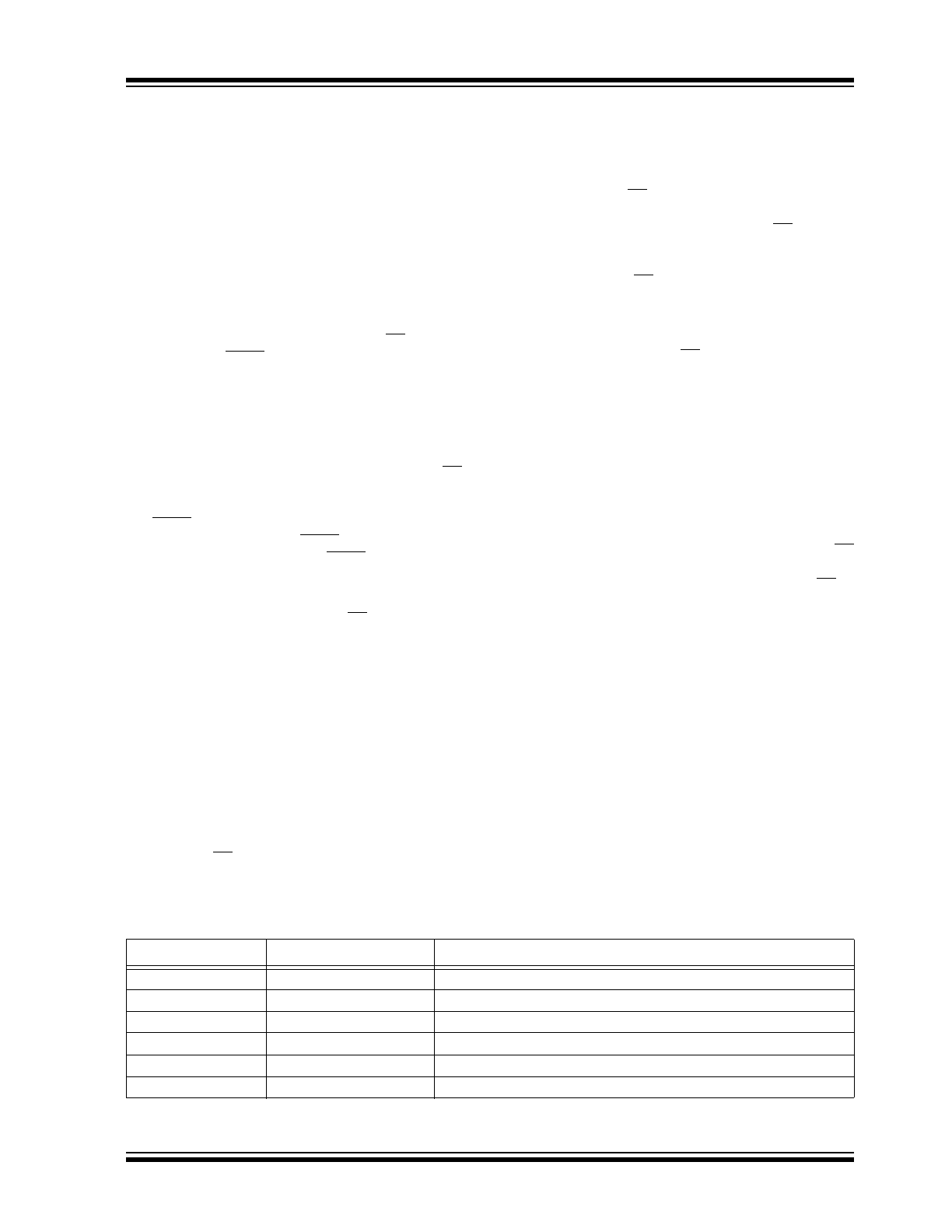
© 2008 Microchip Technology Inc.
DS21223H-page 7
25AA640/25LC640
3.0
FUNCTIONAL DESCRIPTION
3.1
Principles Of Operation
The 25XX640 is a 8192 byte Serial EEPROM designed
to interface directly with the Serial Peripheral Interface
(SPI) port of many of today’s popular microcontroller
families, including Microchip’s PIC16C6X/7X micro-
controllers. It may also interface with microcontrollers
that do not have a built-in SPI port by using discrete
I/O lines programmed properly with the software.
The 25XX640 contains an 8-bit instruction register. The
device is accessed via the SI pin, with data being
clocked in on the rising edge of SCK. The CS pin must
be low and the HOLD pin must be high for the entire
operation.
Table 3-1 contains a list of the possible instruction
bytes and format for device operation. All instructions,
addresses, and data are transferred MSB first, LSB
last.
Data is sampled on the first rising edge of SCK after CS
goes low. If the clock line is shared with other
peripheral devices on the SPI bus, the user can assert
the HOLD input and place the 25XX640 in ‘HOLD’
mode. After releasing the HOLD pin, operation will
resume from the point when the HOLD was asserted.
3.2
Read Sequence
The device is selected by pulling CS low. The 8-bit
READ
instruction is transmitted to the 25XX640 fol-
lowed by the 16-bit address with the three MSBs of the
address being “don’t care” bits. After the correct READ
instruction and address are sent, the data stored in the
memory at the selected address is shifted out on the
SO pin. The data stored in the memory at the next
address can be read sequentially by continuing to pro-
vide clock pulses. The internal Address Pointer is auto-
matically incremented to the next higher address after
each byte of data is shifted out. When the highest
address is reached (1FFFh), the address counter rolls
over to address 0000h allowing the read cycle to be
continued indefinitely. The read operation is terminated
by raising the CS pin (Figure 3-1).
3.3
Write Sequence
Prior to any attempt to write data to the 25XX640 array
or STATUS register, the write enable latch must be set
by issuing the WREN instruction (Figure 3-4). This is
done by setting CS low and then clocking out the
proper instruction into the 25XX640. After all eight bits
of the instruction are transmitted, the CS must be
brought high to set the write enable latch. If the write
operation is initiated immediately after the WREN
instruction without CS being brought high, the data will
not be written to the array because the write enable
latch will not have been properly set.
Once the write enable latch is set, the user may
proceed by setting the CS low, issuing a WRITE
instruction, followed by the address, and then the data
to be written. Up to 32 bytes of data can be sent to the
25XX640 before a write cycle is necessary. The only
restriction is that all of the bytes must reside in the
same page. A page address begins with XXX0 0000
and ends with XXX1 1111. If the internal address
counter reaches XXX1 1111 and the clock continues,
the counter will roll back to the first address of the page
and overwrite any data in the page that may have been
written.
For the data to be actually written to the array, the CS
must be brought high after the Least Significant bit (D0)
of the n
th
data byte has been clocked in. If CS is
brought high at any other time, the write operation will
not be completed. Refer to Figure 3-2 and Figure 3-3
for more detailed illustrations on the byte write
sequence and the page write sequence, respectively.
While the write is in progress, the STATUS register may
be read to check the status of the WPEN, WIP, WEL,
BP1, and BP0 bits (Figure 3-6). A read attempt of a
memory array location will not be possible during a
write cycle. When the write cycle is completed, the
write enable latch is reset.
TABLE 3-1:
INSTRUCTION SET
Instruction Name
Instruction Format
Description
READ
0000 0011
Read data from memory array beginning at selected address
WRITE
0000 0010
Write data to memory array beginning at selected address
WREN
0000 0110
Set the write enable latch (enable write operations)
WRDI
0000 0100
Reset the write enable latch (disable write operations)
RDSR
0000 0101
Read STATUS register
WRSR
0000 0001
Write STATUS register
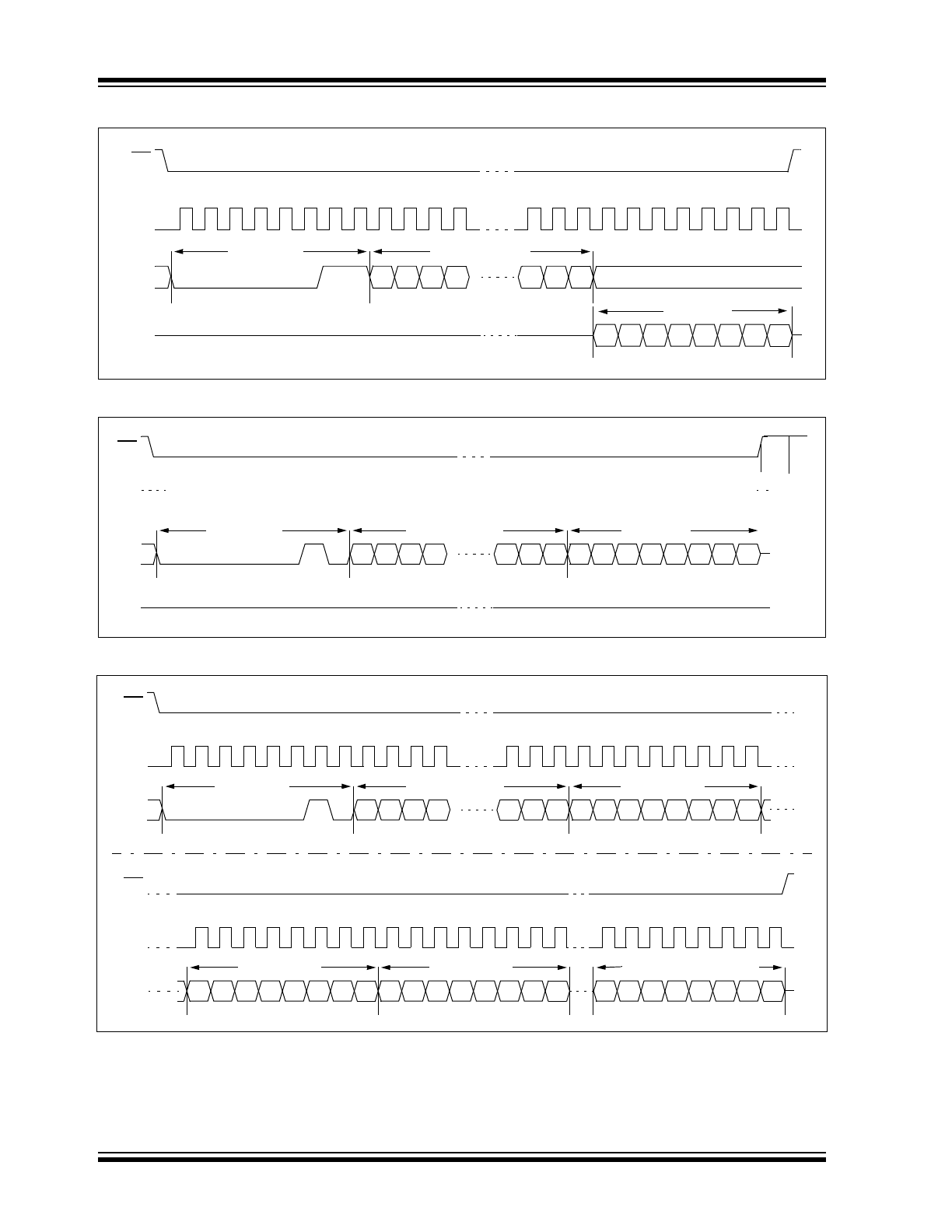
25AA640/25LC640
DS21223H-page 8
© 2008 Microchip Technology Inc.
FIGURE 3-1:
READ SEQUENCE
FIGURE 3-2:
BYTE WRITE SEQUENCE
FIGURE 3-3:
PAGE WRITE SEQUENCE
SO
SI
SCK
CS
0
2
3
4
5
6
7
8
9 10 11
21 22 23 24 25 26 27 28 29 30 31
1
0
1
0
0
0
0
0
1
15 14 13 12
2
1
0
7
6
5
4
3
2
1
0
Instruction
16-bit Address
Data Out
High-Impedance
SO
SI
CS
0
0
0
0
0
0
0
1
15 14 13 12
2
1
0
7
6
5
4
3
2
1
0
Instruction
16-bit Address
Data Byte
High-Impedance
Twc
SI
CS
9 10 11
21 22 23 24 25 26 27 28 29 30 31
0
0
0
0
0
0
0
1
15 14 13 12
2
1
0
7
6
5
4
3
2
1
0
Instruction
16-bit Address
Data Byte 1
SCK
0
2
3
4
5
6
7
1
8
SI
CS
41 42 43
46 47
7
6
5
4
3
2
1
0
Data Byte n (32 max)
SCK
32
34 35 36 37 38 39
33
40
7
6
5
4
3
2
1
0
Data Byte 3
7
6
5
4
3
2
1
0
Data Byte 2
44 45
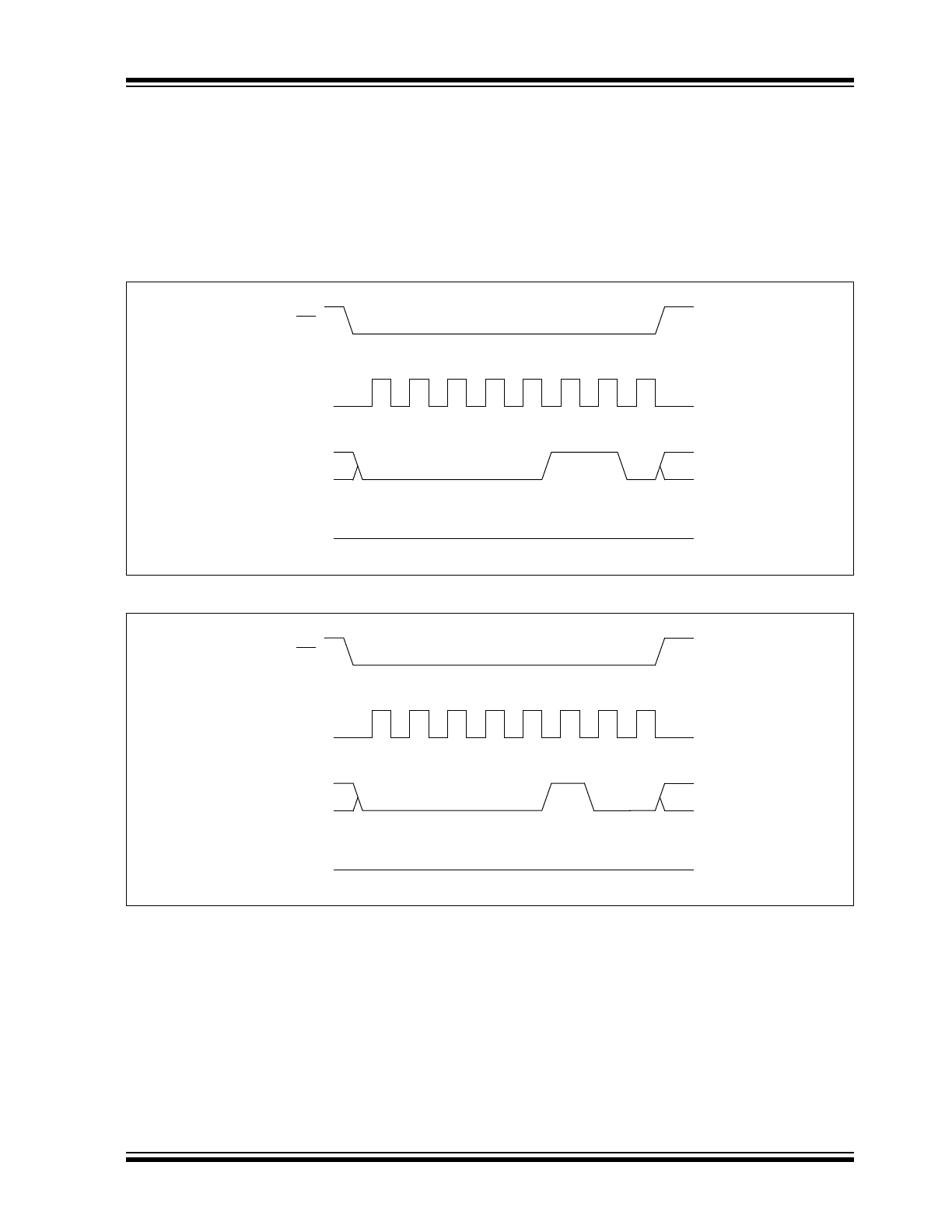
© 2008 Microchip Technology Inc.
DS21223H-page 9
25AA640/25LC640
3.4
Write Enable (WREN) and
Write Disable (WRDI)
The 25XX640 contains a write enable latch. See
Table 3-3 for the Write-Protect Functionality Matrix.
This latch must be set before any write operation will be
completed internally. The WREN instruction will set the
latch, and the WRDI will reset the latch.
The following is a list of conditions under which the
write enable latch will be reset:
• Power-up
• WRDI instruction successfully executed
• WRSR instruction successfully executed
• WRITE instruction successfully executed
FIGURE 3-4:
WRITE ENABLE SEQUENCE
FIGURE 3-5:
WRITE DISABLE SEQUENCE
SCK
0
2
3
4
5
6
7
1
SI
High-Impedance
SO
CS
0
1
0
0
0
0
0
1
SCK
0
2
3
4
5
6
7
1
SI
High-Impedance
SO
CS
0
1
0
0
0
0
0
10
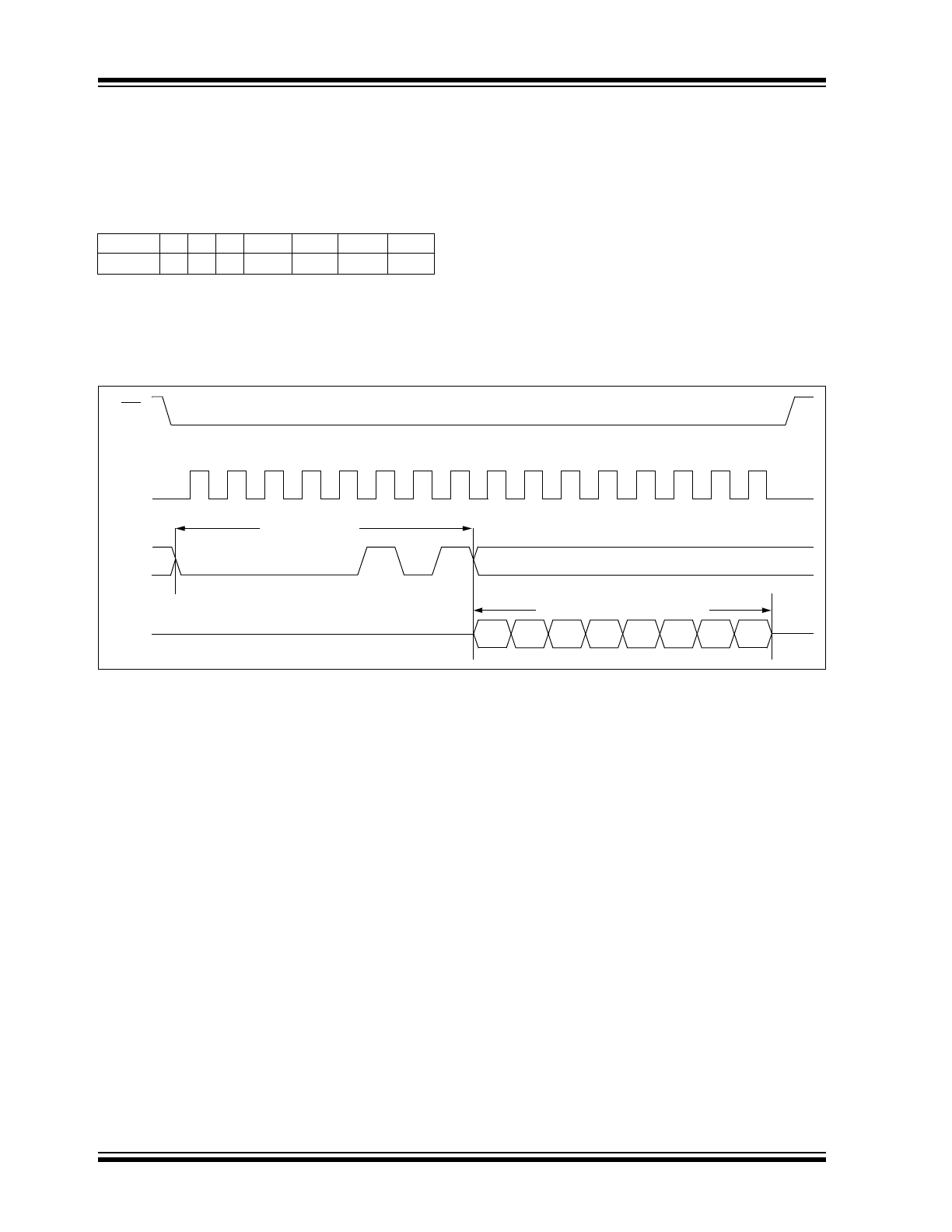
25AA640/25LC640
DS21223H-page 10
© 2008 Microchip Technology Inc.
3.5
Read Status Register Instruction
(RDSR)
The Read Status Register instruction (RDSR) provides
access to the STATUS register. The STATUS register
may be read at any time, even during a write cycle. The
STATUS register is formatted as follows:
The Write-In-Process (WIP) bit indicates whether the
25XX640 is busy with a write operation. When set to a
‘1’, a write is in progress, when set to a ‘0’, no write is
in progress. This bit is read-only.
The Write Enable Latch (WEL) bit indicates the status
of the write enable latch. When set to a ‘1’, the latch
allows writes to the array and STATUS register, when
set to a ‘0’, the latch prohibits writes to the array and
STATUS register. The state of this bit can always be
updated via the WREN or WRDI commands regardless
of the state of write protection on the STATUS register.
This bit is read-only.
The Block Protection (BP0 and BP1) bits indicate
which blocks are currently write-protected. These bits
are set by the user issuing the WRSR instruction. These
bits are nonvolatile.
See Figure 3-6 for RDSR timing sequence.
FIGURE 3-6:
READ STATUS REGISTER TIMING SEQUENCE
7
6
5
4
3
2
1
0
WPEN
X
X
X
BP1
BP0
WEL
WIP
SO
SI
CS
9
10
11
12
13
14
15
1
1
0
0
0
0
0
0
7
6
5
4
2
1
0
Instruction
Data from STATUS Register
High-Impedance
SCK
0
2
3
4
5
6
7
1
8
3